Automatic feeding system of roller kiln
An automatic feeding and roller kiln technology, which is applied to lighting and heating equipment, furnaces, furnace components, etc., can solve problems affecting product quality and output, reducing yield, and wet materials are full, so as to shorten the feeding time, Ensure the accuracy of measurement and prevent the effect of weight exceeding tolerance
- Summary
- Abstract
- Description
- Claims
- Application Information
AI Technical Summary
Problems solved by technology
Method used
Image
Examples
Embodiment Construction
[0012] according to figure 2 with image 3 In the automatic feeding system of the roller kiln shown, a steel frame 1 is supported above the automatic turning line 6 on the entrance side of the roller kiln 11, and a large hopper 2 is installed on the steel frame, and three The weighing unit 3 is fixed on the steel frame, and the lower outlet of the large hopper is equipped with a weighing screw 4 with variable frequency and speed regulation, and a butterfly valve 7 is installed at the outlet of the weighing screw. The large hopper, weighing unit, weighing screw, butterfly valve and The weighing control system together constitutes the metering and weighing system, which is combined in the automatic control system of the roller kiln. A small hopper 8 is installed below the outlet of the weighing screw, and a butterfly valve 7 is housed under the small hopper, and the small hopper stores the charging capacity of a crucible 5 at a time. A synchronous cylinder 10 is installed ahea...
PUM
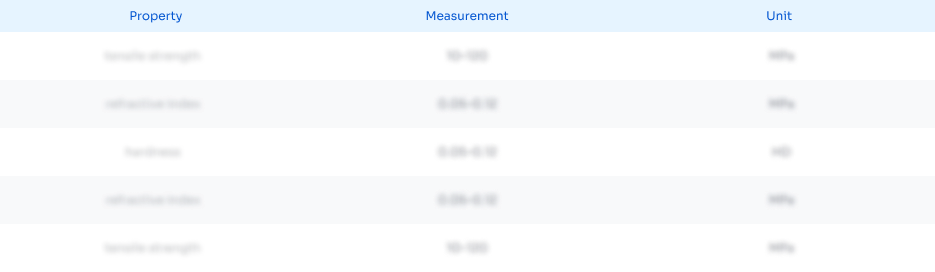
Abstract
Description
Claims
Application Information

- R&D
- Intellectual Property
- Life Sciences
- Materials
- Tech Scout
- Unparalleled Data Quality
- Higher Quality Content
- 60% Fewer Hallucinations
Browse by: Latest US Patents, China's latest patents, Technical Efficacy Thesaurus, Application Domain, Technology Topic, Popular Technical Reports.
© 2025 PatSnap. All rights reserved.Legal|Privacy policy|Modern Slavery Act Transparency Statement|Sitemap|About US| Contact US: help@patsnap.com