Main nozzle structure and weft insertion method of air-jet loom for producing elastic denim
An air-jet loom and main nozzle technology, which is applied in the field of textile processing and manufacturing, can solve the problems of unable to carry weft yarns and easy untwisting of elastic core-spun yarns, and achieve the effects of improving variety adaptability, good product quality and stable operation efficiency.
- Summary
- Abstract
- Description
- Claims
- Application Information
AI Technical Summary
Problems solved by technology
Method used
Image
Examples
Embodiment 1
[0028] figure 1 It is a schematic diagram of the main nozzle structure of the air-jet loom used to produce stretch denim provided by the present invention, and the structure of the main nozzle of the air-jet loom used to produce stretch denim includes a nozzle housing 1, a yarn-guiding core 2 and a yarn-guiding Tube. The yarn drawing core 2 is arranged in the nozzle housing 1 . The yarn guiding tube is a split structure and consists of a fixed end 3 and an adjusting end 4 . One end of the fixed end 3 is connected to the yarn-drawing core 2 , and the other end of the fixed end 3 is bonded seamlessly to the adjusting end 4 . figure 1 Among them, a-a shows the connection between the fixed end 3 of the yarn guide tube and the adjustment end 4, and b-b shows the outlet of the yarn guide tube.
[0029] combine figure 2 , a throat area is formed inside the regulating end of the yarn guide tube, and the outlet of the throat area is the outlet of the yarn guide tube.
[0030] The...
Embodiment 2
[0045] This embodiment differs from embodiment 1 as image 3 As shown, a throat area is formed inside the regulating end of the yarn guide tube, and behind the throat area there is a gradually expanding tapered area, and the exit of the tapered area is the outlet of the yarn guide tube.
[0046] Due to the high quality of the yarn, a certain amount of air flow is required to carry it, so the present invention also sets a gradually expanding tapered area behind the throat at the exit of the yarn guide tube to increase the air flow at the exit. The invention can make the spandex core-spun yarn not only reduce the possibility of being blown away, but also ensure sufficient speed and air flow at the outlet.
Embodiment 3
[0048] This embodiment differs from embodiment 1 as Figure 4 As shown, a throat area is formed inside the adjusting end of the yarn guide tube, and behind the throat area there is a gradually expanding arc area, and the exit of the arc area is the outlet of the yarn guide tube. The side where the arc area is connected to the throat is a small-diameter arc, and the side of the airflow outlet is a large-diameter arc.
[0049] Due to the high quality of the yarn, a certain amount of air flow is required to bear the load, so the present invention also sets a gradually expanding circular arc area behind the throat at the exit of the yarn guide tube to increase the air flow at the exit. The invention can make the spandex core-spun yarn not only reduce the possibility of being blown away, but also ensure sufficient speed and air flow at the outlet.
PUM
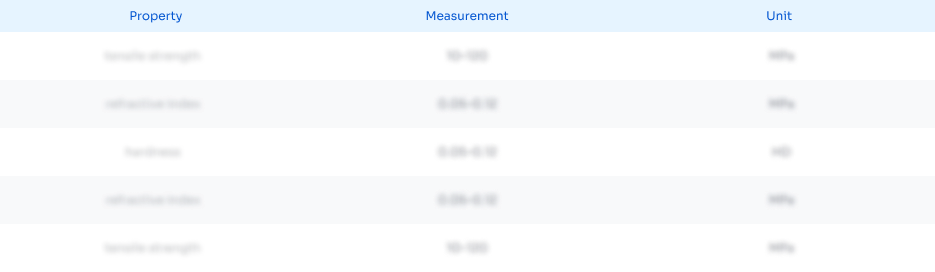
Abstract
Description
Claims
Application Information

- Generate Ideas
- Intellectual Property
- Life Sciences
- Materials
- Tech Scout
- Unparalleled Data Quality
- Higher Quality Content
- 60% Fewer Hallucinations
Browse by: Latest US Patents, China's latest patents, Technical Efficacy Thesaurus, Application Domain, Technology Topic, Popular Technical Reports.
© 2025 PatSnap. All rights reserved.Legal|Privacy policy|Modern Slavery Act Transparency Statement|Sitemap|About US| Contact US: help@patsnap.com