Environment-friendly method for regenerating waste rubber
A waste rubber and waste rubber powder technology, which is applied in the field of waste rubber regeneration, can solve problems such as low sol content, environmental pollution, and a large amount of toxic and harmful substances, and achieve low regeneration temperature, excellent performance, and high regeneration degree.
- Summary
- Abstract
- Description
- Claims
- Application Information
AI Technical Summary
Problems solved by technology
Method used
Image
Examples
no. 1 example
[0026] Put the environmentally friendly desulfurizer mixed with di-tert-butyl disulfide and allicin at a mass ratio of 1:2 and 22-mesh waste tire rubber waste rubber powder into a high-speed mixer at a mass ratio of 2:100 and stir for 15 minutes at a temperature of 120 Celsius, then cool the discharge. Then the waste rubber powder is introduced into the first reaction chamber through the screw conveying device, and then supercritical CO with a pressure of 12 MPa is injected into the first reaction chamber, that is, the swelling chamber where the physical reaction takes place. 2 Fluid, keep the temperature at 150°C, turn on the first screw conveying device, convey the waste rubber powder to the discharge end, the conveying time is 25min, the appropriate residence time is to ensure that the environmentally friendly desulfurizer fully penetrates and disperses in the cross-linked three-dimensional network While conveying, the waste rubber powder can be turned over effectively to a...
no. 2 example
[0028] Put 50-mesh waste EPDM waste rubber powder and environmentally friendly desulfurizer diallyl disulfide into a high-speed mixer at a mass ratio of 100:0.5 and stir for 25 minutes at a stirring temperature of 120°C, then cool and discharge. Then the waste rubber powder is introduced into the first reaction chamber through the conveying device, and then supercritical CO with a pressure of 10 MPa is injected into the second reaction chamber. 2 Fluid, keep the temperature at 160°C, turn on the first screw conveying device, and transport the waste rubber powder to the discharge end for 40 minutes. After the pressure is released, the rubber material enters the second reaction chamber, and the second reaction chamber is opened Microwave heating device with a frequency of 955MHz, an intensity of 0.8KW·h / Kg, a heating temperature of 180°C, and a heating time of 5 minutes. After discharging, it is refined into flakes. Among them, the S-S cross-linking bond of the waste rubber powd...
no. 3 example
[0030] Put waste butyl rubber waste rubber powder and desulfurizer di-tert-butyl disulfide into a high-speed mixer at a mass ratio of 100:0.2 and stir for 30 minutes at a stirring temperature of 70°C, then cool and discharge. Then the waste rubber powder is introduced into the first reaction chamber through a screw conveying device, and then supercritical CO with a pressure of 16 MPa is injected into the chamber. 2 Fluid, keep the temperature at 150°C, turn on the first screw conveying device, and transport the waste rubber powder to the discharge end for 5 minutes, after the pressure is released, the waste rubber powder is transferred to the second reaction chamber, and the second reaction chamber is opened The microwave heating device has a frequency of 2400MHz, an intensity of 1.2KW·h / Kg, a heating temperature of 180°C, and a residence time of waste rubber powder in the second reaction chamber of 30min. Under the action, the waste rubber powder is conveyed to the discharge ...
PUM
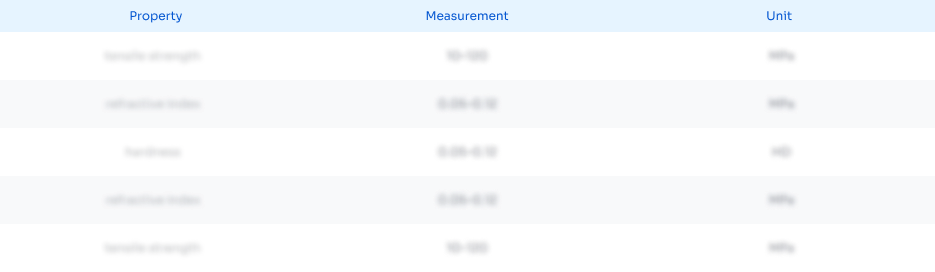
Abstract
Description
Claims
Application Information

- R&D
- Intellectual Property
- Life Sciences
- Materials
- Tech Scout
- Unparalleled Data Quality
- Higher Quality Content
- 60% Fewer Hallucinations
Browse by: Latest US Patents, China's latest patents, Technical Efficacy Thesaurus, Application Domain, Technology Topic, Popular Technical Reports.
© 2025 PatSnap. All rights reserved.Legal|Privacy policy|Modern Slavery Act Transparency Statement|Sitemap|About US| Contact US: help@patsnap.com