Turbine blade profile line design method
A technology of turbine blades and design methods, applied in the direction of blade support elements, calculations, mechanical equipment, etc., can solve problems such as cumbersome calculations and error-prone
- Summary
- Abstract
- Description
- Claims
- Application Information
AI Technical Summary
Problems solved by technology
Method used
Image
Examples
Embodiment Construction
[0033] A kind of design method of turbine blade profile line as shown in Figure 1 to 2, enumerate one bill with the method design of the present invention below, as figure 1 As shown, in any angle triangle OCB, there is a curve tangent to the triangle OCB, that is, OC is the tangent line of the starting point, and BC is the tangent line of the end point, and the equation of this curve is expressed by the following way:
[0034] (x c y-y c x)[(x c -x b )(y-y b )-(y c -y b )(x-x b )]+k(x b y-y b x) 2 =0....(1)
[0035] where x c y-y c x=0 is the equation of OC line segment
[0036] (x c -x b )(y-y b )-(y c -y b )(x-x b )=0 is the equation of BC line segment
[0037] x b y-y b x=0 is the equation of OB line segment
[0038] K is a parameter whose value is determined by the control point D 1 (x 1 ,y 1 ) OK, that is, D 1 (x 1 ,y 1 ) into (1), the value of K can be obtained, but the value of K is cumbersome, we try to make it simpler, and can also show som...
PUM
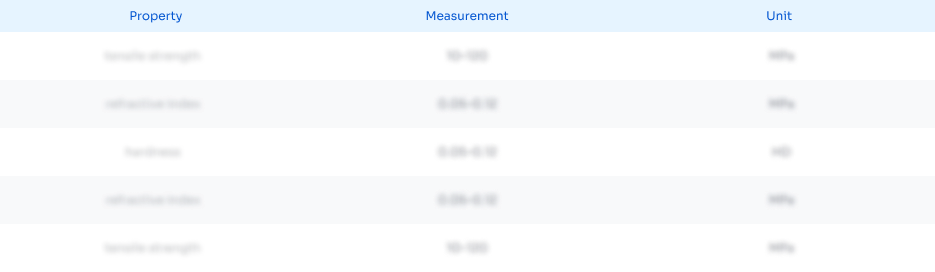
Abstract
Description
Claims
Application Information

- Generate Ideas
- Intellectual Property
- Life Sciences
- Materials
- Tech Scout
- Unparalleled Data Quality
- Higher Quality Content
- 60% Fewer Hallucinations
Browse by: Latest US Patents, China's latest patents, Technical Efficacy Thesaurus, Application Domain, Technology Topic, Popular Technical Reports.
© 2025 PatSnap. All rights reserved.Legal|Privacy policy|Modern Slavery Act Transparency Statement|Sitemap|About US| Contact US: help@patsnap.com