Desulfurization method of alkali solution of liquefied petroleum gas
A technology for liquefied petroleum gas and lye, which is applied in the petroleum industry, gas fuel, fuel, etc., can solve the problems of high energy consumption of redistillation, hidden safety hazards, difficult separation and complete separation, etc., and achieves the effect of improving desulfurization efficiency and reducing sulfur content
- Summary
- Abstract
- Description
- Claims
- Application Information
AI Technical Summary
Problems solved by technology
Method used
Examples
Embodiment 1
[0048] The catalytic liquefied petroleum gas to be treated is the stable liquefied petroleum gas obtained from the MIP process of a refinery affiliated to Sinopec Corporation. The lye used is fresh lye with a sodium hydroxide content of 15%.
[0049] Before mercaptan removal, the lye is treated with nitrogen to remove oxygen, and sintered metal mesh is used as a distributor. When the volume of nitrogen gas introduced is equivalent to 1 times the volume of lye, the process of removing oxygen is completed.
[0050] The desulfurization test was carried out on the desulfurization device in the laboratory. The technological conditions used were: the lye after deoxygenation and the catalytic liquefied petroleum gas were mixed and contacted mechanically in the high-pressure reactor, and the contact temperature was 40°C. The volume ratio of petroleum gas is 1:3.
Embodiment 2
[0052] The catalytic liquefied petroleum gas to be treated is the stable liquefied petroleum gas obtained from the MIP process of a refinery affiliated to Sinopec Corporation. The lye used is fresh lye with a sodium hydroxide content of 15%.
[0053] Add 45% hydrazine hydrate to the lye, and the added amount is 10mg / kg of the lye.
[0054] The desulfurization test was carried out on the desulfurization device in the laboratory. The technological conditions used were: the lye after deoxygenation and the catalytic liquefied petroleum gas were mixed and contacted mechanically in the high-pressure reactor, and the contact temperature was 40°C. The volume ratio of petroleum gas is 1:3.
Embodiment 3
[0061] The coking liquefied petroleum gas to be treated is taken from the stable liquefied gas after the delayed coking process of a refinery affiliated to Sinopec Co., Ltd. is treated with an alcohol-amine composite desulfurizer.
[0062] The alkali agent used is fresh lye, and the sodium hydroxide content is 12%.
[0063] Add 45% hydrazine hydrate to the lye, and the added amount is 10mg / kg of the lye.
[0064] The desulfurization test was carried out on the desulfurization device in the laboratory, and the technological conditions adopted were: the lye after deoxygenation and the catalytic liquefied petroleum gas were in countercurrent contact in the packed tower, the contact temperature was 42°C, the lye and liquefied petroleum gas The volume ratio is 1.5:1, and the liquid hourly volume space velocity of catalytic liquefied petroleum gas is 10h -1 .
PUM
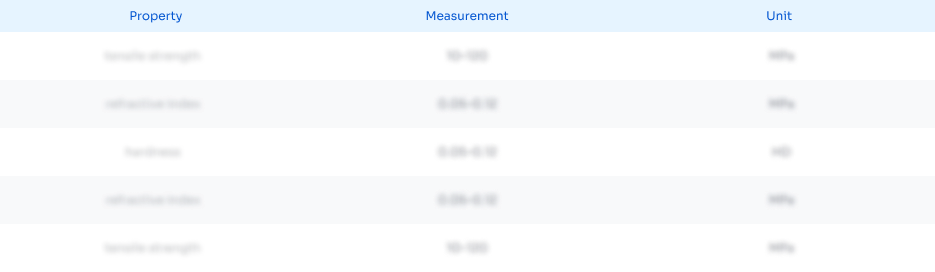
Abstract
Description
Claims
Application Information

- R&D Engineer
- R&D Manager
- IP Professional
- Industry Leading Data Capabilities
- Powerful AI technology
- Patent DNA Extraction
Browse by: Latest US Patents, China's latest patents, Technical Efficacy Thesaurus, Application Domain, Technology Topic, Popular Technical Reports.
© 2024 PatSnap. All rights reserved.Legal|Privacy policy|Modern Slavery Act Transparency Statement|Sitemap|About US| Contact US: help@patsnap.com