Rotary kiln for cement production
A rotary kiln and cement technology, applied in rotary drum furnaces, furnaces, lighting and heating equipment, etc., can solve the problems of welding seam opening, increased use and maintenance costs, thermal expansion and contraction of components, etc., to avoid the fracture of the connection position , The effect of reducing the use and maintenance costs and reducing the maintenance workload
- Summary
- Abstract
- Description
- Claims
- Application Information
AI Technical Summary
Problems solved by technology
Method used
Image
Examples
Embodiment Construction
[0016] In order to better understand the present invention, the embodiments of the present invention will be explained in detail below with reference to the accompanying drawings.
[0017] Such as figure 1 , figure 2 As shown, a rotary kiln for cement production includes a cylindrical barrel 1 coaxially installed on the inner side, a cylindrical cold air jacket 2 on the outer side, and an outer cylindrical surface of the barrel 1 and an inner cylindrical surface of the cold air jacket 2 A connecting structure is provided between the connecting structure. The connecting structure includes a first connecting plate 4 and a second connecting plate 3. The first connecting plate 4 is connected to the cylindrical surface of the kiln shell body, and the second connecting plate 3 is connected to the inside of the cold air jacket. Cylindrical surface connection, the first connecting plate 4 is provided with a first connecting hole 9, the second connecting plate is provided with a second c...
PUM
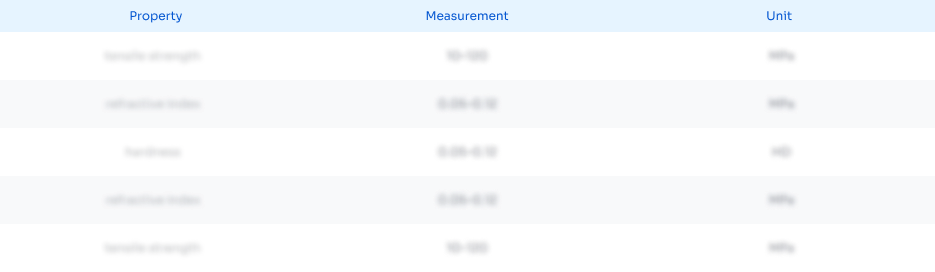
Abstract
Description
Claims
Application Information

- R&D
- Intellectual Property
- Life Sciences
- Materials
- Tech Scout
- Unparalleled Data Quality
- Higher Quality Content
- 60% Fewer Hallucinations
Browse by: Latest US Patents, China's latest patents, Technical Efficacy Thesaurus, Application Domain, Technology Topic, Popular Technical Reports.
© 2025 PatSnap. All rights reserved.Legal|Privacy policy|Modern Slavery Act Transparency Statement|Sitemap|About US| Contact US: help@patsnap.com