Preparation method for multihole fine denier spandex
A technology of fine denier and spandex, which is applied in the field of preparation of porous fine denier spandex, which can solve problems such as being vulnerable to weather erosion, low production efficiency, and limited demand scale, so as to expand the application field and scale of products, improve production efficiency, and prevent adhesion Effect
- Summary
- Abstract
- Description
- Claims
- Application Information
AI Technical Summary
Problems solved by technology
Method used
Image
Examples
Embodiment 1
[0030] Step 1. 237.1kg polytetramethylene ether glycol (molecular weight 1800), 53.9kg 4,4-diphenylmethane diisocyanate are sent to the first reactor at the same time, the reaction time is 2hr, and the reaction temperature is 70°C to obtain the preliminary polymer (PP);
[0031] Step 2. Transport 291kg of prepolymer and 341.5kg of N,N-dimethylacetamide (DMAC) solvent to a high-speed dissolving machine at the same time, and under the action of high-speed shear force, fully dissolve PP to obtain prepolymer solution (PPs);
[0032] Step 3. 632.5kg prepolymer solution and 169.4kg mixed amine DMAC solution (comprising 0.61kg propylenediamine, 4.59kg ethylenediamine, 0.58kg diethylamine, 0.2kg ethanolamine), under the condition of rapid stirring, simultaneously Chain propagation and chain termination occur to prepare a polyallophanate polymer solution;
[0033] Step 4. Add 16.86kg containing antioxidant, lubricant, matting agent, UV absorber in the polyallophanate solution of step...
Embodiment 2
[0037] Step 1. 237.1kg polytetramethylene ether glycol (molecular weight 1800), 54.8kg 4,4-diphenylmethane diisocyanate are sent to the first reactor at the same time, the reaction time is 2hr, and the reaction temperature is 70°C to obtain the preliminary polymer (PP);
[0038] Step 2. Transport 291.8kg of prepolymer and 347.8kg of N,N-dimethylacetamide (DMAC) solvent to the high-speed dissolving machine at the same time, and under the action of high-speed shear force, PP is fully dissolved to obtain the prepolymer Polymer solutions (PPs);
[0039] Step 3. 639.6kg prepolymer solution and 172.5kg mixed amine DMAC solution (comprising 0.59kg propylenediamine, 4.48kg ethylenediamine, 0.51kg diethylamine, 0.21kg ethanolamine), under the condition of rapid stirring, simultaneously Chain propagation and chain termination occur to prepare a polyallophanate polymer solution;
[0040] Step 4. Add 17.12kg containing antioxidant, lubricant, matting agent, UV absorber in the polyalloph...
Embodiment 3
[0044]Step 1. 237.1kg polytetramethylene ether glycol (molecular weight 1800), 54.8kg 4,4-diphenylmethane diisocyanate are sent to the first reactor at the same time, the reaction time is 2hr, and the reaction temperature is 70°C to obtain the preliminary polymer (PP);
[0045] Step 2. Transport 291.8kg of prepolymer and 347.8kg of N,N-dimethylacetamide (DMAC) solvent to the high-speed dissolving machine at the same time, and under the action of high-speed shear force, PP is fully dissolved to obtain the prepolymer Polymer solutions (PPs);
[0046] Step 3. 639.6kg prepolymer solution and 172.5kg mixed amine DMAC solution (comprising 0.55kg propylenediamine, 4.37kg ethylenediamine, 0.49kg diethylamine, 0.39kg ethanolamine), under the condition of rapid stirring, simultaneously Chain propagation and chain termination occur to prepare a polyallophanate polymer solution;
[0047] Step 4. Add 17.55kg containing antioxidant, lubricant, delustering agent, ultraviolet absorber in th...
PUM
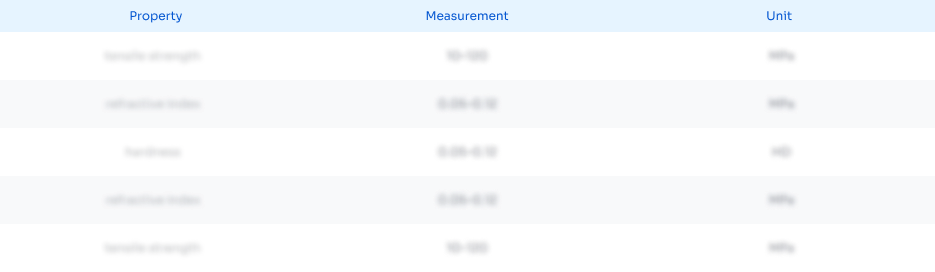
Abstract
Description
Claims
Application Information

- R&D
- Intellectual Property
- Life Sciences
- Materials
- Tech Scout
- Unparalleled Data Quality
- Higher Quality Content
- 60% Fewer Hallucinations
Browse by: Latest US Patents, China's latest patents, Technical Efficacy Thesaurus, Application Domain, Technology Topic, Popular Technical Reports.
© 2025 PatSnap. All rights reserved.Legal|Privacy policy|Modern Slavery Act Transparency Statement|Sitemap|About US| Contact US: help@patsnap.com