A flexible transmission mechanism of a non-enclosed annular rotating body and its application method
A non-enclosed, flexible transmission technology, applied in the field of mechanical automation, to achieve the effect of increasing meshing force and good application prospects
- Summary
- Abstract
- Description
- Claims
- Application Information
AI Technical Summary
Problems solved by technology
Method used
Image
Examples
Embodiment Construction
[0030] The present invention will be further described below in conjunction with the accompanying drawings.
[0031] like figure 1 As shown, a flexible transmission mechanism of a non-closed annular rotating body, including a non-closed annular rotating body 1, a first pinch wheel 2, a first tension wheel 3, a second tension wheel 4, a toothed belt 5, The third tensioning wheel 6, the housing 7, the gear 8, the second pinching wheel 9, the fourth tensioning wheel 10, the fifth tensioning wheel 11, the sixth tensioning wheel 12, and the third pinching wheel 13.
[0032] The first tension wheel 2, the first tension wheel 3, the second tension wheel 4, the third tension wheel 6, the gear 8, the second tension wheel 9, the fourth tension wheel 10, the fifth tension wheel 11. The sixth tensioning wheel 12 and the third pressing wheel 13 have their own mandrels, and all the mandrels are fixed on the bottom plate of the casing 7 . The gear 8, the second tensioning wheel 4, the firs...
PUM
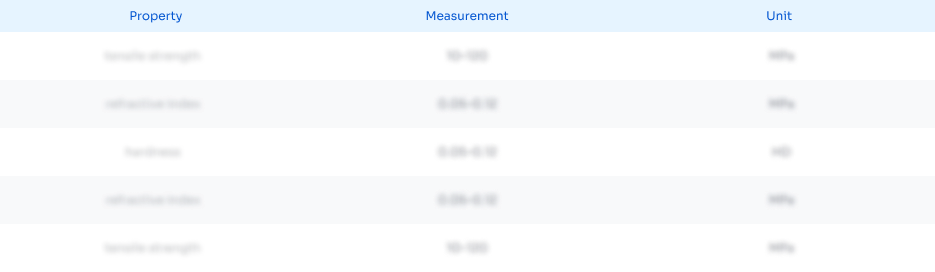
Abstract
Description
Claims
Application Information

- R&D
- Intellectual Property
- Life Sciences
- Materials
- Tech Scout
- Unparalleled Data Quality
- Higher Quality Content
- 60% Fewer Hallucinations
Browse by: Latest US Patents, China's latest patents, Technical Efficacy Thesaurus, Application Domain, Technology Topic, Popular Technical Reports.
© 2025 PatSnap. All rights reserved.Legal|Privacy policy|Modern Slavery Act Transparency Statement|Sitemap|About US| Contact US: help@patsnap.com