Method for producing food-grade zinc sulfate with industrial-grade zinc sulfate as raw material
A zinc sulfate, food-grade technology, applied in directions such as zinc sulfate, can solve the problems of increased production cost, reduced utilization rate of raw materials, human health hazards, etc., and achieves the effects of high production safety, reduced production cost, and shortened production cycle.
- Summary
- Abstract
- Description
- Claims
- Application Information
AI Technical Summary
Problems solved by technology
Method used
Image
Examples
Embodiment 1
[0024] A kind of method that is raw material production food-grade zinc sulfate with technical grade zinc sulfate, comprises the following steps:
[0025] a. Dissolve industrial-grade zinc sulfate in ultrapure water, the weight ratio of material to water is 1:5, fully mix and stir, then filter, and the filtrate is set aside;
[0026] b. Add 0.5% food-grade hydrogen peroxide, 1.0% food-grade activated carbon, and 3% composite bioflocculant to the filtrate obtained in step a, stir and mix thoroughly and ultrasonically treat for 60 minutes, and pass through double filtration. use;
[0027] c. Heat the filtrate obtained in step b to 90°C and concentrate in vacuo for 90 minutes, until microcrystals appear, and the stirrer speed is 20r / min;
[0028] d. Cooling and crystallization, the agitator is 15r / min, centrifugal separation, after drying, food-grade zinc sulfate is obtained, and the solution is recycled to step a for use.
[0029] The comprehensive yield rate of the product ob...
Embodiment 2
[0031] a. Dissolve industrial-grade zinc sulfate in ultrapure water, the weight ratio of material to water is 1:4, fully mix and stir, then filter, and the filtrate is set aside;
[0032] b. Add 0.8% food-grade hydrogen peroxide, 0.8% food-grade diatomaceous earth and 2% composite biological flocculant to the filtrate obtained in step a, stir and mix thoroughly and ultrasonically treat for 90 minutes, filter through sand core and Microfiltration double filtration, the filtrate is ready for use;
[0033] c. Heat the filtrate obtained in step b to 80°C and concentrate in vacuo for 120 minutes until microcrystals appear, and the stirrer speed is 20r / min;
[0034] d. Cooling and crystallization, the agitator is 15r / min, centrifugal separation, after drying, food-grade zinc sulfate is obtained, and the solution is recycled to step a for use.
[0035] The comprehensive yield rate of the product obtained by the method is 75.1%, and the technical indicators of the product all exceed ...
Embodiment 3
[0037] a. Dissolve industrial-grade zinc sulfate in ultrapure water, the weight ratio of material to water is 1:5, fully mix and stir, then filter, and the filtrate is set aside;
[0038] b. Add 0.8% food-grade hydrogen peroxide, 0.8% food-grade activated carbon, and 3% composite bioflocculant to the filtrate obtained in step a, stir and mix thoroughly, ultrasonicate for 60 minutes, pass double filtration, and the filtrate is ready for use ;
[0039] c. Heat the filtrate obtained in step b to 85°C and concentrate in vacuo for 100 minutes until microcrystals appear, and the stirrer speed is 20r / min;
[0040] d. Cooling and crystallization, the agitator is 15r / min, centrifugal separation, after drying, food-grade zinc sulfate is obtained, and the solution is recycled to step a for use.
[0041] The comprehensive yield rate of the product obtained by the method is 73.6%, and the technical indicators of the product all exceed the requirements of the national standard.
PUM
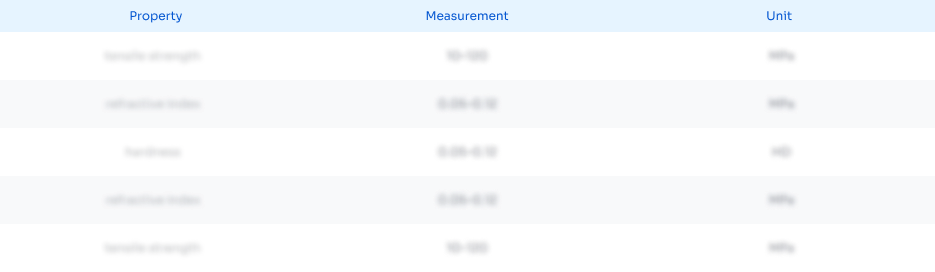
Abstract
Description
Claims
Application Information

- R&D Engineer
- R&D Manager
- IP Professional
- Industry Leading Data Capabilities
- Powerful AI technology
- Patent DNA Extraction
Browse by: Latest US Patents, China's latest patents, Technical Efficacy Thesaurus, Application Domain, Technology Topic, Popular Technical Reports.
© 2024 PatSnap. All rights reserved.Legal|Privacy policy|Modern Slavery Act Transparency Statement|Sitemap|About US| Contact US: help@patsnap.com