Method for preparing cyclopentane by hydrogenation of cyclopentadiene or preparing methyl cyclopentane by hydrogenation of methyl cyclopentadiene
A technology for methylcyclopentadiene and methylcyclopentane is applied in the field of hydrogenation of cyclopentadiene to produce cyclopentane or the hydrogenation of methylcyclopentadiene to produce methylcyclopentane, which can solve the problem of unfavorable industrialization. Cost and process operation difficulty, increase of refining and separation process, large solvent loss and other problems, to achieve the effect of reducing the phenomenon of hydrogenated raw rubber, high yield and strong anti-colloid ability
- Summary
- Abstract
- Description
- Claims
- Application Information
AI Technical Summary
Problems solved by technology
Method used
Image
Examples
Embodiment 1
[0027] The control conditions of the reactor 3 are reaction inlet temperature 105°C, reaction pressure 4.0MPag, 3 layers of bed 4, temperature rise of each bed layer 35°C, hydrogen-oil ratio 100, reaction oil phase space velocity 35h -1 .
[0028] Using cyclopentadiene (unpolymerized) produced by the upstream device as the raw material, the mass content of (cyclopentadiene + methylcyclopentadiene) is 99.73%, and the reaction results are shown in Table 1:
[0029] Table I
[0030]
Embodiment 2
[0032] The control conditions of the reactor 3 are reaction inlet temperature 105°C, reaction pressure 4.0MPag, 3 layers of bed 4, temperature rise of each bed layer 35°C, hydrogen-oil ratio 100, reaction oil phase space velocity 35h -1 .
[0033] Using the methylcyclopentadiene (unpolymerized) produced by the upstream device as the raw material, the mass content of (cyclopentadiene + methylcyclopentadiene) is 99.88%. The reaction results are shown in Table 2:
[0034] Table II
[0035]
Embodiment 3
[0037] The control conditions of the reactor 3 are reaction inlet temperature 10°C, reaction pressure 0.5MPag, 4 layers of bed 4, temperature rise of each bed layer 28°C, hydrogen-oil ratio 300, reaction oil phase space velocity 15h -1 .
[0038] Using cyclopentadiene (unpolymerized) produced by the upstream device as the raw material, the mass content of (cyclopentadiene + methylcyclopentadiene) is 99.61%. The reaction results are shown in Table 3:
[0039] Table three
PUM
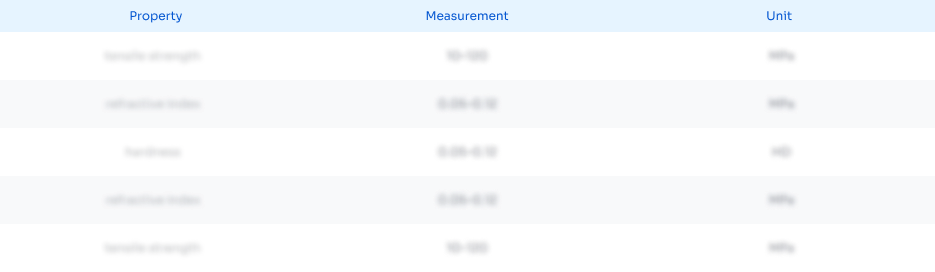
Abstract
Description
Claims
Application Information

- Generate Ideas
- Intellectual Property
- Life Sciences
- Materials
- Tech Scout
- Unparalleled Data Quality
- Higher Quality Content
- 60% Fewer Hallucinations
Browse by: Latest US Patents, China's latest patents, Technical Efficacy Thesaurus, Application Domain, Technology Topic, Popular Technical Reports.
© 2025 PatSnap. All rights reserved.Legal|Privacy policy|Modern Slavery Act Transparency Statement|Sitemap|About US| Contact US: help@patsnap.com