Spray absorption type system for simultaneous desulphurization and denitration of sintering flue gas
A technology for desulfurization, denitrification, and sintering flue gas, which is applied in the fields of air quality improvement, combined device, and dispersed particle separation. Cost, low cost effect
- Summary
- Abstract
- Description
- Claims
- Application Information
AI Technical Summary
Problems solved by technology
Method used
Image
Examples
Embodiment Construction
[0031] The present invention will be further described below in conjunction with the accompanying drawings.
[0032] like figure 1 Shown is a spray absorption sintering flue gas simultaneous desulfurization and denitrification system, including flue gas reaction and purification system, new solution addition system and recirculation solution system.
[0033] The flue gas reaction and purification system includes a first bag filter 1, a spray absorption tower 2, a second bag filter 3 and a chimney 4; the gas outlet of the first bag filter 1 is connected to the flue gas inlet of the spray absorption tower 2, and the spray The flue gas outlet of the absorption tower 2 is connected to the gas inlet of the second bag filter 3, and the gas outlet of the second bag filter 3 is connected to the chimney 4; wherein the flue gas inlet of the spray absorption tower 2 is set in the middle of the spray absorption tower 2, in the The top of the spray absorption tower 2 is provided with a sp...
PUM
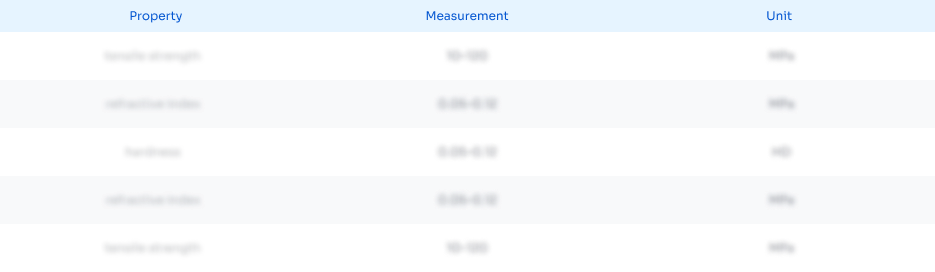
Abstract
Description
Claims
Application Information

- Generate Ideas
- Intellectual Property
- Life Sciences
- Materials
- Tech Scout
- Unparalleled Data Quality
- Higher Quality Content
- 60% Fewer Hallucinations
Browse by: Latest US Patents, China's latest patents, Technical Efficacy Thesaurus, Application Domain, Technology Topic, Popular Technical Reports.
© 2025 PatSnap. All rights reserved.Legal|Privacy policy|Modern Slavery Act Transparency Statement|Sitemap|About US| Contact US: help@patsnap.com