Feature-based automatic groove feature grouping machining method for plate parts
An automatic grouping and slot feature technology, applied in instruments, computer control, simulators, etc., can solve the problems of cumbersome programming process and low programming efficiency, achieve high reliability, improve enterprise work efficiency, and save craftsman time.
- Summary
- Abstract
- Description
- Claims
- Application Information
AI Technical Summary
Problems solved by technology
Method used
Image
Examples
Embodiment Construction
[0028] The present invention will be further described below in conjunction with accompanying drawings and examples.
[0029] Such as Figure 1-5 shown.
[0030] A feature-based automatic grouping processing method for groove features of plate parts, the flow chart of which is shown in figure 1 As shown, the specific steps are as follows:
[0031] Step 1: Read the part CAM model. In the CAM environment, import the three-dimensional solid model of the part, and at the same time import the tool library information provided by the user and the NC process regulations.
[0032] Step 2: Read part features and create a list of part feature recognition results. The feature recognition result list is the result of feature recognition, which records the feature information contained in the part, including the groove feature, hole feature, rib feature, corner feature, etc. of the part. Plate parts are mainly groove and hole features. A groove feature consists of a horizontal web fa...
PUM
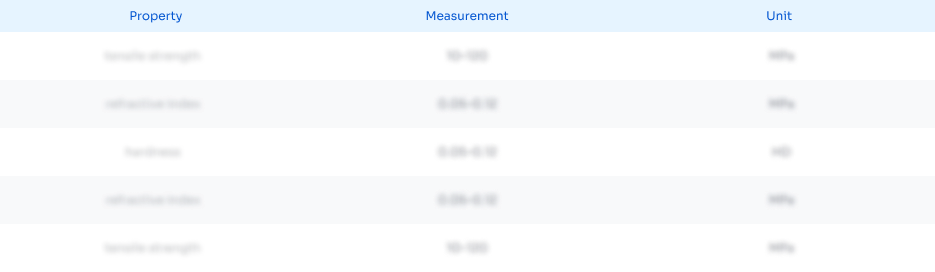
Abstract
Description
Claims
Application Information

- R&D Engineer
- R&D Manager
- IP Professional
- Industry Leading Data Capabilities
- Powerful AI technology
- Patent DNA Extraction
Browse by: Latest US Patents, China's latest patents, Technical Efficacy Thesaurus, Application Domain, Technology Topic, Popular Technical Reports.
© 2024 PatSnap. All rights reserved.Legal|Privacy policy|Modern Slavery Act Transparency Statement|Sitemap|About US| Contact US: help@patsnap.com