Ultrasonic frequency induction heating technology based quick hot-dipping aluminizing technology
A technology of induction heating and hot infiltration, applied in the direction of metal material coating process, coating, solid diffusion coating, etc., can solve the problems of surface brittleness, lack of surface, high cost of aluminized steel parts, and achieve bending performance and stamping. Improved formability, improved thermal shock resistance and thermal fatigue resistance, reduced concentration and consumption
- Summary
- Abstract
- Description
- Claims
- Application Information
AI Technical Summary
Problems solved by technology
Method used
Examples
Embodiment 1
[0018] A super-audio frequency induction heating rapid hot dip aluminizing process is as follows:
[0019] ① Degreasing: chemically degrease the steel parts, bake and degrease them at 400°C for 10 minutes, until the surface is clean and free of oil;
[0020] ② Pickling and rust removal: Take the degreased steel parts out of the heating furnace, immerse them in a mixed pickling solution containing 2% sulfuric acid, 15% hydrochloric acid, and the balance is water, and equipped with a current generating device. After 2~ Take out the steel parts after 3 minutes of quick pickling;
[0021] ③Water washing: wash the steel parts after derusting with high-pressure water for 1~2 times;
[0022] ④ Surface activation: Immediately immerse the rinsed steel piece in an activation solution containing 1.8% anhydrous sodium tetraborate, 2% sodium nitrite, 30% sodium hydroxide, and the balance is water for 30 seconds;
[0023] ⑤. Permeation aid: Take out the activated steel piece and immed...
Embodiment 2
[0027] A super-audio frequency induction heating rapid hot dip aluminizing process is as follows:
[0028] ①, Degreasing: Chemically degrease the steel parts, bake and degrease at 500°C for 5 minutes, until the surface is clean and free of oil;
[0029] ②. Rapid pickling and rust removal: take the degreased steel parts out of the heating furnace, immerse them in a mixed pickling solution containing 2% sulfuric acid, 15% hydrochloric acid, and the balance is water, and equipped with a current generating device. After 2 Remove the steel part after ~3 minutes of pickling;
[0030] ③Water washing: wash the steel parts after derusting with high-pressure water for 1~2 times;
[0031] ④ Surface activation: Immediately immerse the rinsed steel piece in an activation solution containing 1.8% anhydrous sodium tetraborate, 2% sodium nitrite, 30% sodium hydroxide, and the balance is water for 30 seconds;
[0032] ⑤ Permeation aid: Take out the activated steel piece and immediately i...
PUM
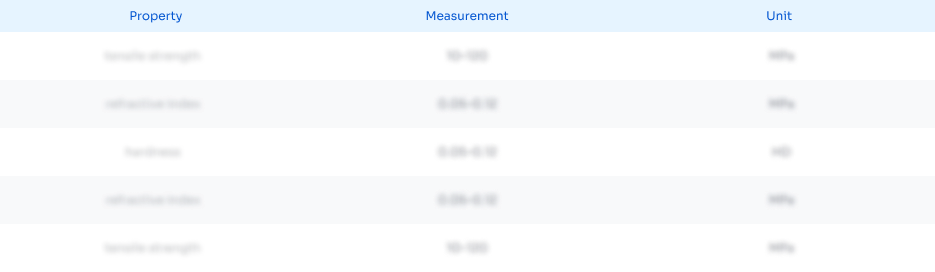
Abstract
Description
Claims
Application Information

- R&D
- Intellectual Property
- Life Sciences
- Materials
- Tech Scout
- Unparalleled Data Quality
- Higher Quality Content
- 60% Fewer Hallucinations
Browse by: Latest US Patents, China's latest patents, Technical Efficacy Thesaurus, Application Domain, Technology Topic, Popular Technical Reports.
© 2025 PatSnap. All rights reserved.Legal|Privacy policy|Modern Slavery Act Transparency Statement|Sitemap|About US| Contact US: help@patsnap.com