Method for predicting fluid-solid coupled characteristic value of elastic hydrofoil
A fluid-structure coupling and prediction method technology, applied in special data processing applications, electrical digital data processing, instruments, etc., can solve the problems of elastic hydrofoil flow field structure and dynamic characteristics, lack of elastic hydrofoil numerical prediction method, etc.
- Summary
- Abstract
- Description
- Claims
- Application Information
AI Technical Summary
Problems solved by technology
Method used
Image
Examples
Embodiment 1
[0040] A numerical prediction method for fluid-solid coupling characteristics of elastic hydrofoils, such as figure 1 As shown, it is mainly realized by the following steps:
[0041] Step 1: Establish a two-dimensional watershed and hydrofoil geometric model
[0042] For a given hydrofoil, a two-dimensional watershed and hydrofoil geometric model is established in the pre-processing software ICEM CFD. The material of the hydrofoil is POM, and the main material properties are: elastic modulus E=3000MPa, density ρ=1480kg / s, Poisson's ratio 0.35. The elastic deformation of the hydrofoil is simplified as follows: figure 2 As shown: one end of the hydrofoil is fixed, and the other end is a free end. The elastic deformation of the hydrofoil along the span direction is ignored, and only the vibration deformation h of the section of the free end along the vertical direction and the rotational deformation θ around the central axis are considered.
[0043] Step 2: 2D watershed grid ...
PUM
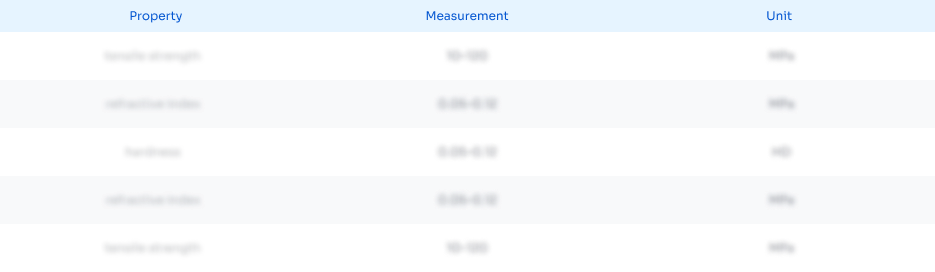
Abstract
Description
Claims
Application Information

- Generate Ideas
- Intellectual Property
- Life Sciences
- Materials
- Tech Scout
- Unparalleled Data Quality
- Higher Quality Content
- 60% Fewer Hallucinations
Browse by: Latest US Patents, China's latest patents, Technical Efficacy Thesaurus, Application Domain, Technology Topic, Popular Technical Reports.
© 2025 PatSnap. All rights reserved.Legal|Privacy policy|Modern Slavery Act Transparency Statement|Sitemap|About US| Contact US: help@patsnap.com