A kind of end tooth structure fretting fatigue test device and test method
A technology of fretting fatigue and test equipment, which is applied in the testing of machine gears/transmission mechanisms, testing the strength of materials by applying repetitive force/pulsation force, and testing the strength of materials by applying stable tension/pressure, which can solve the problems of fatigue life decline, Problems such as the small driving force of the thread loading scheme and the change of the loading normal force can achieve the effect of reducing the test cost, saving the cost of the test piece, and increasing the driving force.
- Summary
- Abstract
- Description
- Claims
- Application Information
AI Technical Summary
Problems solved by technology
Method used
Image
Examples
Embodiment Construction
[0045] Please refer to Figure 1 to Figure 7 As shown, the end tooth structure fretting fatigue test device of the present invention includes a concave tooth fixing assembly 1 , a convex tooth clamping assembly 2 and a normal force loading assembly 3 .
[0046] The concave tooth fixing assembly 1 includes an upper clamp body 12 and a concave tooth test piece 11 installed on the upper clamp body 12, an M10 compression bolt 13 and a concave tooth pressure plate 14, wherein the upper clamp body 12 includes a hollow lower part 120 and a lower part. The upper part 121 above 120, wherein the upper end of the upper part 121 can be clamped on the upper chuck 43 of a common uniaxial fatigue testing machine, and is integrated with the upper crossbeam 41 of the testing machine, and can be raised and lowered in the vertical direction thereupon. The lower part 120 is formed with a rectangular hole 122 penetrating through the front, rear and lower surfaces of the lower part 120 . A rectang...
PUM
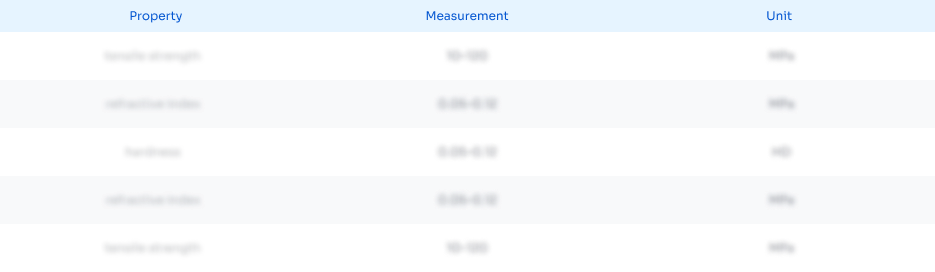
Abstract
Description
Claims
Application Information

- R&D
- Intellectual Property
- Life Sciences
- Materials
- Tech Scout
- Unparalleled Data Quality
- Higher Quality Content
- 60% Fewer Hallucinations
Browse by: Latest US Patents, China's latest patents, Technical Efficacy Thesaurus, Application Domain, Technology Topic, Popular Technical Reports.
© 2025 PatSnap. All rights reserved.Legal|Privacy policy|Modern Slavery Act Transparency Statement|Sitemap|About US| Contact US: help@patsnap.com