Manufacturing method of mask plate opening for organic light-emitting display device
A technology for a light-emitting display and a manufacturing method, which are applied in vacuum evaporation plating, ion implantation plating, metal material coating processes, etc., can solve the problems affecting the edge quality of an organic deposition layer, poor straightness of the opening edge of a small opening, and the like, Achieving the effect of good edge quality, guaranteed edge quality and excellent deposition effect
- Summary
- Abstract
- Description
- Claims
- Application Information
AI Technical Summary
Problems solved by technology
Method used
Image
Examples
Embodiment Construction
[0030] Embodiments of the present invention are described in detail below, examples of which are shown in the drawings, wherein the same or similar reference numerals denote the same or similar elements or elements having the same or similar functions. The embodiments described below by referring to the figures are exemplary only for explaining the present invention and should not be construed as limiting the present invention.
[0031] The inventive idea of the present invention is as follows: in the prior art, in order to overcome the evaporation effect during the evaporation process of the organic material of the organic light-emitting display, and to overcome the influence of the edge of the mask plate on the evaporation of the organic material, the mask plate is usually prepared by an etching process. "concave" openings, but this process has a relatively large impact on the environment; there is a process to prepare "concave-shaped" structural openings by laser cutting, ...
PUM
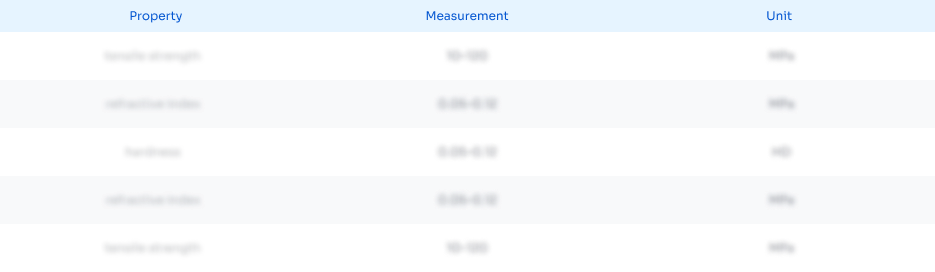
Abstract
Description
Claims
Application Information

- R&D
- Intellectual Property
- Life Sciences
- Materials
- Tech Scout
- Unparalleled Data Quality
- Higher Quality Content
- 60% Fewer Hallucinations
Browse by: Latest US Patents, China's latest patents, Technical Efficacy Thesaurus, Application Domain, Technology Topic, Popular Technical Reports.
© 2025 PatSnap. All rights reserved.Legal|Privacy policy|Modern Slavery Act Transparency Statement|Sitemap|About US| Contact US: help@patsnap.com