Petroleum resin modified rosin resin dispersion
A technology of petroleum resin and modified rosin, which is applied in the direction of mineral oil hydrocarbon copolymer adhesives, graft polymer adhesives, adhesive types, etc., and can solve the problems of poor performance such as peeling force and holding force , to achieve the effect of good fluidity and low degree of fusion
- Summary
- Abstract
- Description
- Claims
- Application Information
AI Technical Summary
Problems solved by technology
Method used
Image
Examples
Embodiment 1
[0025] Raw materials and dosage
[0026] Rosin 47.0kg; Maleic anhydride 2.0kg; Nonylphenol sulfide oligomer 0.12kg; Propylene glycol 0.9kg; Petroleum resin 12.0kg; 0.5mol / L potassium hydroxide aqueous solution 0.15kg; 55.0kg of pure water at 90°C;
[0027] The production steps are:
[0028] A. Grind the rosin, put it into the reactor, under CO 2 Heat and melt under protection, and then start the stirring system. When the temperature reaches 190°C, add maleic anhydride and keep warm at 195°C for 1.5h to 2.5h;
[0029] B. After step A, continue to add the above-mentioned nonylphenol sulfide oligomer, propylene glycol, petroleum resin and 0.5mol / L potassium hydroxide aqueous solution into the reaction kettle under stirring conditions, and then heat up to 260°C for heat preservation. and continuously measure its acid value;
[0030] C. When the acid value of the reaction materials in the reaction kettle of the B step=125mgKOH / g, cool down to 100°C, put in a hydrophilic reag...
Embodiment 2
[0032] Raw materials and dosage
[0033] Rosin 48.0kg; Maleic anhydride 2.2kg; Nonylphenol sulfide oligomer 0.16kg; Propylene glycol 1.0kg; Petroleum resin 13.0kg; 0.5mol / L potassium hydroxide aqueous solution 0.17kg; 58.0kg of purified water at 95°C;
[0034] The production steps are:
[0035] A. Grind the rosin, put it into the reactor, under CO 2 Heat and melt under protection, and then start the stirring system. When the temperature reaches 193°C, add maleic anhydride and keep it at 205°C for 2 hours;
[0036] B. After step A, continue to add the above-mentioned nonylphenol sulfide oligomer, propylene glycol, petroleum resin and 0.5mol / L potassium hydroxide aqueous solution into the reaction kettle under stirring conditions, and then heat up to 270°C for heat preservation. and continuously measure its acid value;
[0037] C. When the acid value of the reaction material in the reaction kettle in the step B is 130mgKOH / g, cool down to 130°C, put in a hydrophilic reage...
Embodiment 3
[0039] Raw materials and dosage
[0040] Rosin 50.0kg; Maleic anhydride 2.5kg; Nonylphenol sulfide oligomer 0.18kg; Propylene glycol 1.1kg; Petroleum resin 13.5kg; 0.5mol / L potassium hydroxide aqueous solution 0.18kg; 60.0kg of pure water at 98℃;
[0041] The production steps are:
[0042] A. Grind the rosin, put it into the reactor, under CO 2 Heat and melt under protection, then start the stirring system, when the temperature reaches 195°C, add maleic anhydride, and keep warm at 210°C for 2.5h;
[0043] B. After step A, continue to add the above-mentioned nonylphenol sulfide oligomer, propylene glycol, petroleum resin and 0.5mol / L potassium hydroxide aqueous solution into the reaction kettle under stirring conditions, and then heat up to 285°C for heat preservation. and continuously measure its acid value;
[0044]C. When the acid value of the reaction materials in the reaction kettle in the step B is 126mgKOH / g, cool down to 150°C, put in a hydrophilic reagent, then ...
PUM
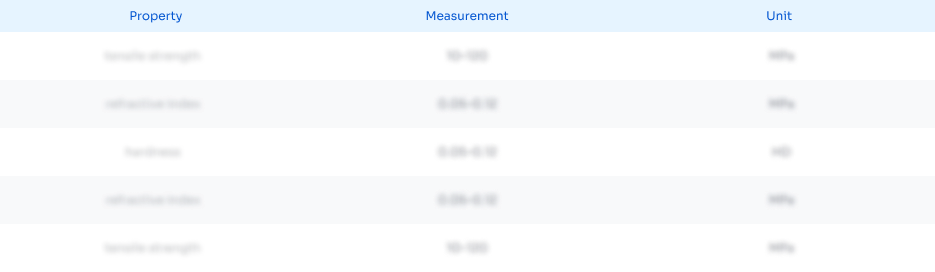
Abstract
Description
Claims
Application Information

- R&D
- Intellectual Property
- Life Sciences
- Materials
- Tech Scout
- Unparalleled Data Quality
- Higher Quality Content
- 60% Fewer Hallucinations
Browse by: Latest US Patents, China's latest patents, Technical Efficacy Thesaurus, Application Domain, Technology Topic, Popular Technical Reports.
© 2025 PatSnap. All rights reserved.Legal|Privacy policy|Modern Slavery Act Transparency Statement|Sitemap|About US| Contact US: help@patsnap.com