Precision casting method for column crystal guide vanes of gas turbine
A technology of guide vanes and gas turbines, applied to casting molding equipment, casting molds, casting mold components, etc., can solve problems such as difficult processes, and achieve the effects of improving pass rate and large economic benefits
- Summary
- Abstract
- Description
- Claims
- Application Information
AI Technical Summary
Problems solved by technology
Method used
Image
Examples
Embodiment 1
[0035] A method for preparing a large-sized, complex-shaped, near-net-shape directional guide vane. The total length of the guide vane is 170mm, and the length of the blade body is 100mm. Figure 4 Design precision casting module, crystal pulling height is 220mm. EC95 was used to prepare the formwork, the calcination temperature of the formwork was 1450°C, the pouring temperature was 1550°C, and the pouring completion time was 5-10 s. After the pouring is completed, from bottom to top, first pull the mold shell 1020mm at a pulling speed of 15mm / min in order to fully select the crystal; then pull the mold shell 40mm at a pulling speed of 12mm / min; finally pull the mold shell at a pulling speed of 8mm / min The pulling speed is 160mm to pull the mold shell, and the mold shell is stretched completely.
[0036]
Embodiment 2
[0038] Preparation method of near-net-shape 1-stage oriented columnar guide vane for a certain gas turbine. The total length of the guide vane is 181mm, and the length of the blade body is 77mm. Figure 4 Design precision casting module, crystal pulling height is 230mm. EC95 was used to prepare the formwork, the calcination temperature of the formwork was 1500°C, the pouring temperature was 1550°C, and the pouring completion time was 5-10 s. After the pouring is completed, from bottom to top, the shell is first drawn at a drawing speed of 20mm / min to fully select crystals; then the drawing speed is reduced to 10mm / min; finally the drawing speed is 8mm / min.
[0039]
Embodiment 3
[0041] Preparation method of near-net-shape 1-stage oriented columnar guide vane for a certain gas turbine. The total length of the guide vane is 290mm, and the length of the blade body is 180mm. Figure 4Design precision casting module, crystal pulling height is 330mm. EC95 was used to prepare the formwork, the calcination temperature of the formwork was 1500°C, the pouring temperature was 1500°C, and the pouring completion time was 5-10 s. After pouring is completed, from bottom to top, the shell is first drawn at a drawing speed of 20mm / min to fully select crystals; then the drawing speed is reduced to 10mm / min; finally the drawing speed is 8mm / min.
PUM
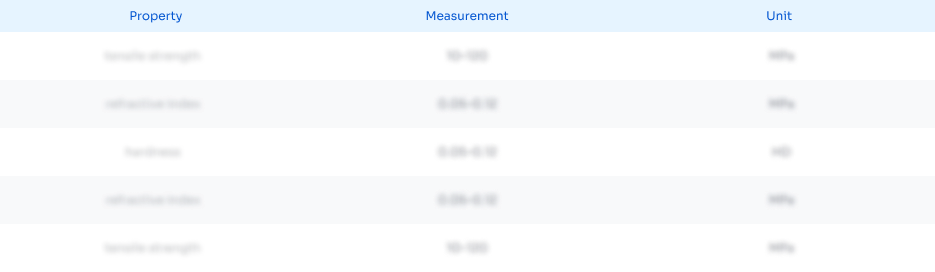
Abstract
Description
Claims
Application Information

- R&D
- Intellectual Property
- Life Sciences
- Materials
- Tech Scout
- Unparalleled Data Quality
- Higher Quality Content
- 60% Fewer Hallucinations
Browse by: Latest US Patents, China's latest patents, Technical Efficacy Thesaurus, Application Domain, Technology Topic, Popular Technical Reports.
© 2025 PatSnap. All rights reserved.Legal|Privacy policy|Modern Slavery Act Transparency Statement|Sitemap|About US| Contact US: help@patsnap.com