Two ends flaring forming technique of cylindrical barrels
A cylindrical barrel, the technology of molding process, applied in the direction of bicycle accessories, transportation and packaging, etc.
- Summary
- Abstract
- Description
- Claims
- Application Information
AI Technical Summary
Problems solved by technology
Method used
Image
Examples
Embodiment Construction
[0017] In this embodiment, the machining process of the inner cylinder of a motorcycle muffler is taken as an example.
[0018] First, the raw material is directly expanded into the sheet material 1, and holes 11 are punched on the sheet material. The use of the sheet material will reduce the stretching deformation of the raw material during molding. Then hit U again to make the sheet material 1 become a U-shaped body 2. When hitting the U, make the end of the sheet material face down to form a flat surface at both ends. At the same time as the flat surface, the stepped bosses 21 at both ends are formed into Good, therefore, this reduces many processes such as first rolling, then flattening, and expanding both ends; finally, putting in the rolling mold, adding the mandrel and then rolling, welding straight seams after rolling, forming a cylindrical shape Cylinder 3.
[0019] In this embodiment, one end of the U-shaped body has a boss, the other end has two legs, and the arc of the...
PUM
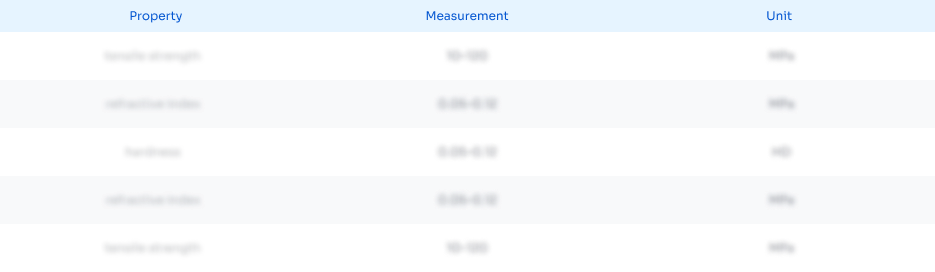
Abstract
Description
Claims
Application Information

- R&D Engineer
- R&D Manager
- IP Professional
- Industry Leading Data Capabilities
- Powerful AI technology
- Patent DNA Extraction
Browse by: Latest US Patents, China's latest patents, Technical Efficacy Thesaurus, Application Domain, Technology Topic, Popular Technical Reports.
© 2024 PatSnap. All rights reserved.Legal|Privacy policy|Modern Slavery Act Transparency Statement|Sitemap|About US| Contact US: help@patsnap.com