Control circuit of inside diameter slicing machine
A technology of inner circle slicing and control circuit, applied in the direction of program control, digital control, electrical program control, etc., can solve the problems of low efficiency and high cost of slicing processing, achieve high processing accuracy, avoid errors, and achieve the effect of precise control
- Summary
- Abstract
- Description
- Claims
- Application Information
AI Technical Summary
Problems solved by technology
Method used
Image
Examples
Embodiment 1
[0054] This embodiment provides a control circuit for an inner circle slicer, such as figure 1 Shown, including:
[0055] The general control module 1 inputs corresponding control instructions to the first control module 2, the stepper motor driver module 3, and the second control module 4 according to the processing requirements.
[0056] The first control module 2 is connected to the stepper motor driver module 3 and is used to control the on and off of the stepper motor driver module 3; the stepper motor driver module 3 is used to drive the stepper motor to rotate, And then drive the worktable on the inner circle slicer to produce corresponding displacement.
[0057] The cutter head assembly 5 includes two or more cutter heads, and a motor connected to each cutter head and controlling the rotation of the cutter head, and each cutter head corresponds to a material rod installed on the worktable.
[0058] The second control module 4 is connected to the motor in the cutter head assemb...
Embodiment 2
[0071] On the basis of embodiment 1, the inner circle slicer control circuit described in this embodiment, such as figure 2 As shown, the power supply module 6 includes a transformer and a switching power supply.
[0072] The primary winding end of the transformer obtains AC voltage from the power grid to supply power to the first control module 2, the stepper motor driver module 3, the second control module 4 and the cutter head assembly 5.
[0073] The switching power supply is connected to the secondary winding end of the transformer, and the step-down AC voltage obtained from the secondary winding end is converted into a 24V direct current voltage; and the output end of the switching power supply is connected to the total The voltage receiving end of the control module 1 is connected to provide 24V DC voltage to it.
[0074] In the inner circle slicer control circuit of this embodiment, the power supply module 6 includes a transformer and a switching power supply. After the prim...
PUM
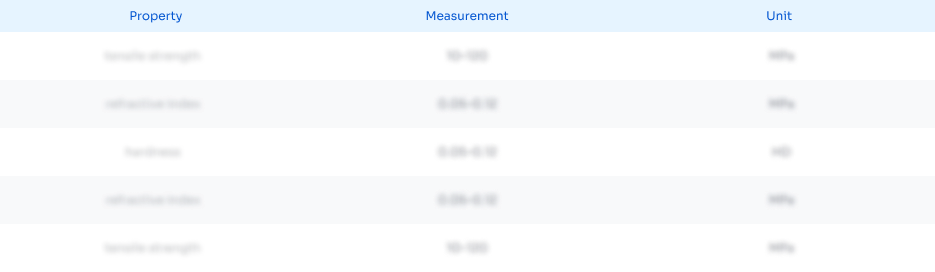
Abstract
Description
Claims
Application Information

- R&D Engineer
- R&D Manager
- IP Professional
- Industry Leading Data Capabilities
- Powerful AI technology
- Patent DNA Extraction
Browse by: Latest US Patents, China's latest patents, Technical Efficacy Thesaurus, Application Domain, Technology Topic, Popular Technical Reports.
© 2024 PatSnap. All rights reserved.Legal|Privacy policy|Modern Slavery Act Transparency Statement|Sitemap|About US| Contact US: help@patsnap.com