Method and system for detecting and displaying structural damage to pipelines
A pipeline and damage technology, which is applied in the field of pipeline structure damage detection, can solve the problems of inability to meet the high-precision requirements of long-distance pipelines, the limited movable distance of the ring sensor group, and low monitoring efficiency, so as to avoid detection blind spots and strong practicability and versatility, the effect of cost reduction
- Summary
- Abstract
- Description
- Claims
- Application Information
AI Technical Summary
Problems solved by technology
Method used
Image
Examples
Embodiment Construction
[0026] In order to make the purpose of the present invention clearer, the present invention will be further described in detail below in conjunction with the accompanying drawings and embodiments. It should be understood that the specific embodiments described here are only used to explain the present invention, not to limit the present invention.
[0027]As a guided wave, Lamb wave has the advantages of long propagation distance, strong penetrating power, low attenuation, and sensitivity to damaged surfaces of various types of structures, and is suitable for damage detection of pipeline structures. When the Lamb wave propagates in the pipeline structure, reflection or signal attenuation will occur when the pipeline structure changes significantly (such as defects such as cracks, corrosion or delamination). The waveform signal characteristics such as the waveform amplitude and frequency of the Lamb wave detection signal will change. In the method for detecting and displaying ...
PUM
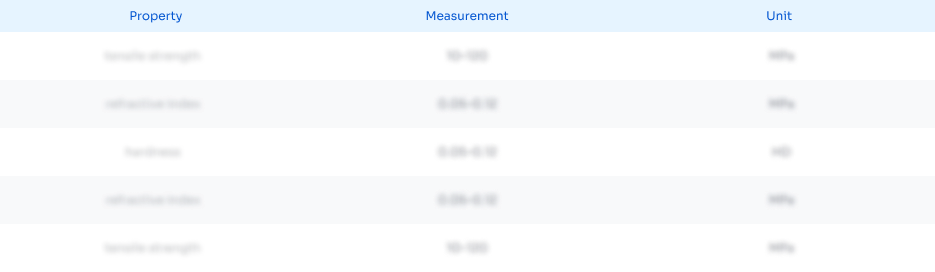
Abstract
Description
Claims
Application Information

- R&D Engineer
- R&D Manager
- IP Professional
- Industry Leading Data Capabilities
- Powerful AI technology
- Patent DNA Extraction
Browse by: Latest US Patents, China's latest patents, Technical Efficacy Thesaurus, Application Domain, Technology Topic, Popular Technical Reports.
© 2024 PatSnap. All rights reserved.Legal|Privacy policy|Modern Slavery Act Transparency Statement|Sitemap|About US| Contact US: help@patsnap.com