Double-side cooling concentric tube-in-tube type sulfonating reactor
A technology of sulfonation reactors and concentric sleeves, applied in chemical instruments and methods, chemical/physical processes, etc., can solve problems such as temperature out of control, long production cycle, increased by-products, etc., to achieve easy temperature control and pressure bearing capacity Strong, large heat transfer area
- Summary
- Abstract
- Description
- Claims
- Application Information
AI Technical Summary
Problems solved by technology
Method used
Image
Examples
Embodiment
[0035] This embodiment is an application example of the present invention in the sulfonation of m-nitrobenzene with sulfur trioxide in liquid phase.
[0036] Three double-sided cooling concentric sleeve-type sulfonation reactors, the diameter of the reaction sleeve is DN25, and the effective reaction length is 1.2m; they are connected in series to form the initial sulfonation reactor, and then eight SK-type static mixers of DN20 are connected in series. A single pipe is 1.2m long; it serves as a sustaining reactor. During the experiment, the reaction temperature was controlled at 90°C±5°C, the flow rate of m-nitrobenzene was 200L / h, and the flow rate of sulfur trioxide was 100L / h. The experimental results showed that the content of liquid m-nitrobenzenesulfonic acid was 96.5%, and the mass of nitrosulfone Content 2.5%.
[0037] The experimental results show that the reactor can quickly remove the heat of reaction, the reaction temperature can be controlled sensitively, the pr...
PUM
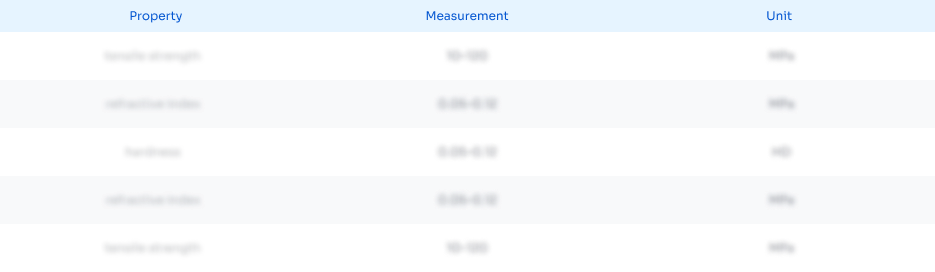
Abstract
Description
Claims
Application Information

- Generate Ideas
- Intellectual Property
- Life Sciences
- Materials
- Tech Scout
- Unparalleled Data Quality
- Higher Quality Content
- 60% Fewer Hallucinations
Browse by: Latest US Patents, China's latest patents, Technical Efficacy Thesaurus, Application Domain, Technology Topic, Popular Technical Reports.
© 2025 PatSnap. All rights reserved.Legal|Privacy policy|Modern Slavery Act Transparency Statement|Sitemap|About US| Contact US: help@patsnap.com