Self-gain-scheduling PID (proportion integration differentiation) controller of double-in double-out system of heat-engine plant
A self-dispatching, thermal power plant technology, applied in the direction of adaptive control, general control system, control/regulation system, etc., can solve the problems of time-consuming, labor-intensive, unable to achieve differential predictive control, etc., to reduce dynamic deviation and static deviation , Shorten the transition time, the effect of fast parameter setting
- Summary
- Abstract
- Description
- Claims
- Application Information
AI Technical Summary
Problems solved by technology
Method used
Image
Examples
Embodiment Construction
[0019] see figure 1 , figure 1 It is a simplified structural diagram of the gain self-scheduling PID controller of the dual-input and double-output system of the thermal power plant of the present invention.
[0020] A gain self-scheduling PID controller for a dual-input and double-output system in a thermal power plant, comprising: a fast control loop 10, a fast loop detection regulator 20, a slow control loop 30, a slow loop detection regulator 40, and a fast loop feedforward controller 17 , fast loop feedforward and feedback integrated computing unit 16, slow loop feedforward controller 37, slow loop feedforward and feedback integrated computing unit 36, first actuator and second actuator;
[0021] The fast control loop 10 includes a fast loop PID gain self-scheduling controller 11 and a fast loop control mode switch 15, and the PID input end of the fast loop control mode switch 15 is connected to the fast loop PID gain self-scheduling controller 11 The output end, its ON...
PUM
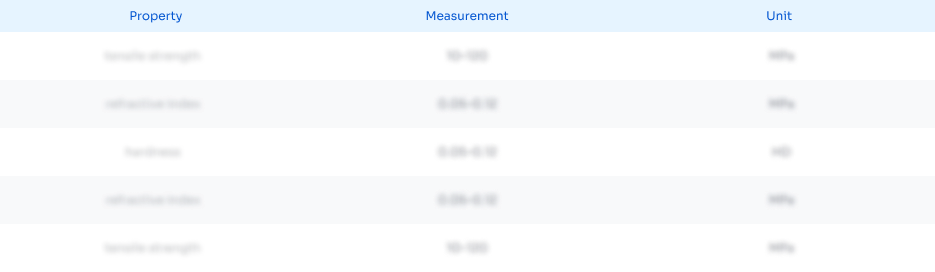
Abstract
Description
Claims
Application Information

- R&D Engineer
- R&D Manager
- IP Professional
- Industry Leading Data Capabilities
- Powerful AI technology
- Patent DNA Extraction
Browse by: Latest US Patents, China's latest patents, Technical Efficacy Thesaurus, Application Domain, Technology Topic, Popular Technical Reports.
© 2024 PatSnap. All rights reserved.Legal|Privacy policy|Modern Slavery Act Transparency Statement|Sitemap|About US| Contact US: help@patsnap.com