System and method for detecting surface defects of large-caliber spherical optical element
A technology of spherical optics and detection system
- Summary
- Abstract
- Description
- Claims
- Application Information
AI Technical Summary
Problems solved by technology
Method used
Image
Examples
Embodiment
[0079] A surface flaw detection test was carried out on the surface of a large-aperture spherical optical element. During the inspection, the selected large-aperture spherical optical element to be tested has a caliber of φ160mm, a spherical curvature radius R of 200mm, and a detection microscope with a field of view of f s It is φ15mm. Under the constraints of invariant rules along the latitude, the sub-aperture distribution is planned according to the trajectory of the latitude and longitude. During planning, the overlapping area between the sub-apertures in the latitude direction is f s / 4, take the overlap coefficient k=1.1 in the meridian direction, then the distribution of each sub-aperture on the spherical surface can be calculated according to formula 3, and obtained after three-dimensional simulation Image 6 The subaperture planning image shown. A total of 63 sub-apertures are planned. As can be seen from the figure, the sub-apertures are evenly distributed and co...
PUM
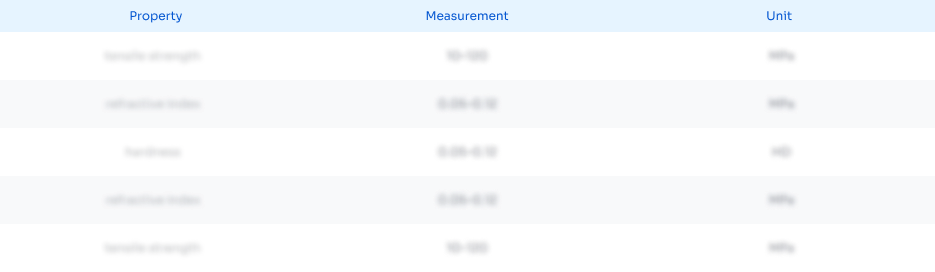
Abstract
Description
Claims
Application Information

- R&D Engineer
- R&D Manager
- IP Professional
- Industry Leading Data Capabilities
- Powerful AI technology
- Patent DNA Extraction
Browse by: Latest US Patents, China's latest patents, Technical Efficacy Thesaurus, Application Domain, Technology Topic, Popular Technical Reports.
© 2024 PatSnap. All rights reserved.Legal|Privacy policy|Modern Slavery Act Transparency Statement|Sitemap|About US| Contact US: help@patsnap.com