Pass system and roughing process for avoiding cracks on surface of large-size round steel
A surface crack and large-scale technology, applied in the field of metallurgy, can solve problems such as surface cracks, achieve the effects of improving the formation probability, avoiding instability, and avoiding surface cracks
- Summary
- Abstract
- Description
- Claims
- Application Information
AI Technical Summary
Problems solved by technology
Method used
Image
Examples
Embodiment 1
[0014] The finished product specification of 320mm×480mm rectangular billet is φ130mmSAE4137 large-size round steel. The rough rolling pass system is designed as follows: the pass system is composed of pass Ⅰ, pass Ⅱ and pass Ⅲ. Among them, the groove bottom width dimension b of pass type I and pass type II k The ratios to the width B of the incoming material entering the pass for the first time are 1.043 and 1.033, respectively. Groove bottom width dimension b of pass type III k The difference from the incoming width B is 1mm. Hole slot width B k Satisfies the relationship: B k =b+△. Where b is the maximum width of the rolled piece out of the pass. The widening allowances △ of the three pass types are 12mm, 5mm and 5mm respectively. Roll gap S=0.021×roll diameter D. Hole height h k =(notch width B k - groove bottom width b k ) / pass sidewall slope tanψ+roll gap S, where the values of the three pass sidewall slopes tanψ are 26.7%, 18.0% and 13.3%, respectively. Gro...
Embodiment 2
[0016] The finished product specification of 320mm×480mm rectangular billet is φ150mm25MnCrNiMo large-size round steel. The rough rolling pass system is designed as follows: the pass system is composed of pass type Ⅰ, pass type Ⅱ and pass type Ⅲ. Among them, the groove bottom width dimension b of pass type I and pass type II k The ratios to the width B of the incoming material entering the pass for the first time are 1.043 and 1.033, respectively. Groove bottom width dimension b of pass type III k The difference from the incoming width B is 1mm. Hole slot width B k Satisfies the relationship: B k =b+△. Where b is the maximum width of the rolled piece out of the pass. The widening allowances △ of the three pass types are 12mm, 5mm and 5mm respectively. Roll gap S=0.021×roll diameter D. Hole height h k =(notch width B k - groove bottom width b k ) / pass sidewall slope tanψ+roll gap S, where the values of the three pass sidewall slopes tanψ are 26.7%, 18.0% and 13.3%, ...
PUM
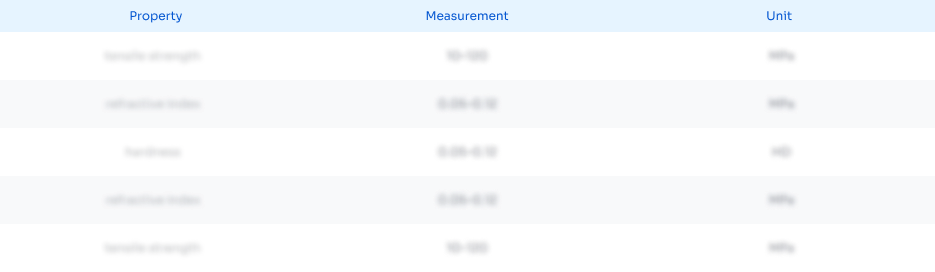
Abstract
Description
Claims
Application Information

- R&D
- Intellectual Property
- Life Sciences
- Materials
- Tech Scout
- Unparalleled Data Quality
- Higher Quality Content
- 60% Fewer Hallucinations
Browse by: Latest US Patents, China's latest patents, Technical Efficacy Thesaurus, Application Domain, Technology Topic, Popular Technical Reports.
© 2025 PatSnap. All rights reserved.Legal|Privacy policy|Modern Slavery Act Transparency Statement|Sitemap|About US| Contact US: help@patsnap.com