An assembly and welding process for multimedia wire rods and an automatic assembly and welding machine
An automatic assembly and assembly welding technology, applied in the direction of connection, line/collector parts, electrical components, etc., can solve the problems of increasing the production burden of enterprises and unstable quality, so as to save manpower and man hours, reduce production costs, and compact structure Effect
- Summary
- Abstract
- Description
- Claims
- Application Information
AI Technical Summary
Problems solved by technology
Method used
Image
Examples
Embodiment Construction
[0028] The invention provides an assembly and welding process of multimedia wires and an automatic assembly welding machine, which greatly improves the welding efficiency of multimedia wires, saves manpower and labor hours, saves production costs, and improves the welding quality of multimedia wires.
[0029] The technical solution in the present invention will be clearly and completely described below in conjunction with the accompanying drawings in the present invention. Obviously, what is described is only a part of the embodiments of the present invention, not all the embodiments. Based on the embodiments of the present invention, all other embodiments obtained by persons of ordinary skill in the art without making creative efforts belong to the protection scope of the present invention.
[0030] combine figure 1 As shown, an assembly and welding process of multimedia wire mainly includes the following steps:
[0031] (1) The feeding is fixed and the wire ends are trimmed...
PUM
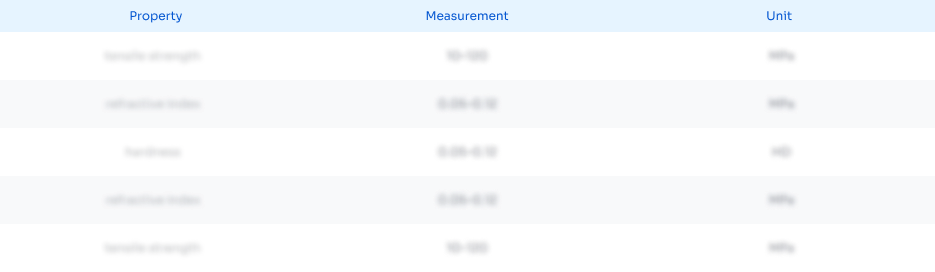
Abstract
Description
Claims
Application Information

- R&D Engineer
- R&D Manager
- IP Professional
- Industry Leading Data Capabilities
- Powerful AI technology
- Patent DNA Extraction
Browse by: Latest US Patents, China's latest patents, Technical Efficacy Thesaurus, Application Domain, Technology Topic, Popular Technical Reports.
© 2024 PatSnap. All rights reserved.Legal|Privacy policy|Modern Slavery Act Transparency Statement|Sitemap|About US| Contact US: help@patsnap.com