One-bath desizing and dyeing method of polyester pulp-containing fabric and its special auxiliary agent
A dyeing method and technology of bath auxiliaries, applied in the direction of dyeing method, textile and paper making, dry cleaning fiber products, etc., can solve the problems of strong dye selectivity, large dye selectivity, and inability to dye, and achieve low energy consumption and sewage discharge. Low, short process effect
- Summary
- Abstract
- Description
- Claims
- Application Information
AI Technical Summary
Problems solved by technology
Method used
Image
Examples
Embodiment 1
[0049] Embodiment 1, preparation of one-bath auxiliaries for desizing and dyeing polyester sizing fabric
[0050] According to the ratio (wt%) of each component shown in Table 1, one-bath additive A and one-bath additive B were prepared.
[0051] Formulation of different embodiment formulas of table 1
[0052]
[0053] The wetting emulsifier in the scheme 1 is a mixture of emulsifier TO7, emulsifier TO3, isomeric trideceth phosphate TEP and secondary alkylsulfonate sodium SAS60, wherein, the emulsifier TO7, emulsifier The mass parts of TO3, isomeric trideceth polyether phosphate TEP and secondary alkyl sulfonate sodium SAS60 are 25, 15, 30 and 30 in sequence; the leveling and diffusing agent is isopropyl phthalimide, A mixture of glyceryl ether polyoxyethylene ether (average EO = 20) oleate and styrene phenol polyoxyethylene ether (average EO = 17) ammonium sulfate, of which, isopropyl phthalimide, glyceryl ether The mass parts of polyoxyethylene ether (average EO=20) ole...
Embodiment 2
[0061] Embodiment 2, one-bath process of desizing and dyeing polyester pulp-containing fabrics using one-bath auxiliary agent A and one-bath auxiliary agent B
[0062] The process flow of the present invention: enter 3000kg of water into the dyeing machine → enter the fabric → add a bath of auxiliary agent A → add dye after 10 minutes of circulation → heat up to 130°C at a rate of 1.5°C / min after 10 minutes of circulation → keep warm for 50 minutes → cool down to 85°C → For every liter of water, add one-bath additive B and hydrosulfite, carry out reduction cleaning at 85°C for 30 minutes → drain, wash in warm water at 50°C for 15 minutes → discharge the cloth.
[0063] The factory currently uses conventional process flow: dyeing machine into 3000kg of water→ into 300kg of fabric→add 15kg of sodium hydroxide, 3kg of chelating dispersant FK-422D3, 3kg of wetting agent FK-st15, 3kg of desizing agent FK-608→heat up to 100°C, keep warm for 20min→cool down, drain→water inflow→heat u...
PUM
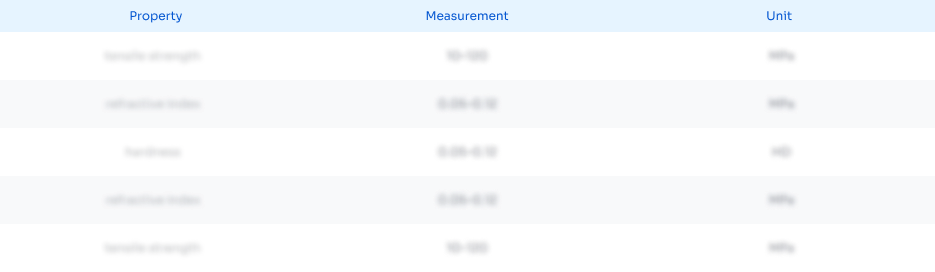
Abstract
Description
Claims
Application Information

- Generate Ideas
- Intellectual Property
- Life Sciences
- Materials
- Tech Scout
- Unparalleled Data Quality
- Higher Quality Content
- 60% Fewer Hallucinations
Browse by: Latest US Patents, China's latest patents, Technical Efficacy Thesaurus, Application Domain, Technology Topic, Popular Technical Reports.
© 2025 PatSnap. All rights reserved.Legal|Privacy policy|Modern Slavery Act Transparency Statement|Sitemap|About US| Contact US: help@patsnap.com