Preparation method of filter material
A technology of filter material and process steps, which is applied in the field of filter material preparation, can solve problems such as failure to meet requirements, and achieve the effects of low manufacturing cost, effective filtration, and good filtering effect
- Summary
- Abstract
- Description
- Claims
- Application Information
AI Technical Summary
Problems solved by technology
Method used
Examples
Embodiment 1
[0011] Embodiment one: a kind of preparation method of filter material, comprises the following processing steps, and component ratio is weight parts:
[0012] (1) Treat activated carbon and zeolite at 350°C for 10 hours to form a porous structure;
[0013] (2) Heat the epoxy resin at 80°C for 24 hours, and then wash it with 0.1mol / L dilute hydrochloric acid to make the epoxy resin porous;
[0014] (3) Mix 50 parts of epoxy resin after step (2), 5 parts of activated carbon after step (1), 5 parts of zeolite after step (1), 5 parts of negative ion powder and 1 part of adhesive Stir well to obtain a clay-like mixture;
[0015] (4) Molding the clay-like mixture obtained in step (3) in a mold to obtain a filter body; air-drying the filter body at room temperature for 12 hours to obtain the filter material.
Embodiment 2
[0016] Embodiment two: a kind of preparation method of filter material, comprises the following processing steps, and component ratio is weight parts:
[0017] (1) Treat activated carbon and zeolite at 500°C for 5 hours to form a porous structure;
[0018] (2) Heat the epoxy resin at 100°C for 12 hours, and then rinse with 0.2mol / L dilute hydrochloric acid to make the epoxy resin porous;
[0019] (3) Mix 90 parts of epoxy resin after step (2), 25 parts of activated carbon after step (1), 10 parts of zeolite after step (1), 10 parts of negative ion powder and 5 parts of adhesive Stir well to obtain a clay-like mixture;
[0020] (4) Molding the clay-like mixture obtained in step (3) in a mold to obtain a filter body; air-drying the filter body at room temperature for 24 hours to obtain the filter material.
Embodiment 3
[0021] Embodiment three: a kind of preparation method of filter material, comprises following process step, and component ratio is weight parts:
[0022] (1) Treat activated carbon and zeolite at 400°C for 8 hours to form a porous structure;
[0023] (2) Heat the epoxy resin at 90°C for 18 hours, and then wash it with 0.15mol / L dilute hydrochloric acid to make the epoxy resin porous;
[0024] (3) Mix 60 parts of epoxy resin after step (2), 15 parts of activated carbon after step (1), 6 parts of zeolite after step (1), 6 parts of negative ion powder and 4 parts of adhesive Stir well to obtain a clay-like mixture;
[0025] (4) Molding the clay-like mixture obtained in step (3) in a mold to obtain a filter body; air-drying the filter body at room temperature for 18 hours to obtain the filter material.
PUM
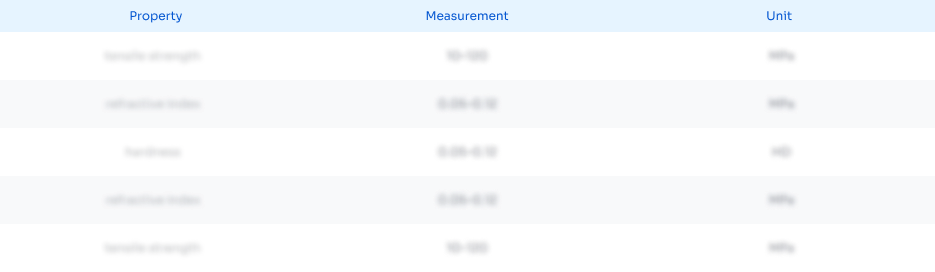
Abstract
Description
Claims
Application Information

- R&D
- Intellectual Property
- Life Sciences
- Materials
- Tech Scout
- Unparalleled Data Quality
- Higher Quality Content
- 60% Fewer Hallucinations
Browse by: Latest US Patents, China's latest patents, Technical Efficacy Thesaurus, Application Domain, Technology Topic, Popular Technical Reports.
© 2025 PatSnap. All rights reserved.Legal|Privacy policy|Modern Slavery Act Transparency Statement|Sitemap|About US| Contact US: help@patsnap.com