Lignite upgrading treatment device
A processing device and technology for lignite, applied in special forms of dry distillation, petroleum industry, coke ovens, etc., can solve the problems of small hot air path, low thermal efficiency, easy to ignite and burn, etc., to extend the hot air path, improve thermal efficiency, and prevent adverse effects. Effect
- Summary
- Abstract
- Description
- Claims
- Application Information
AI Technical Summary
Problems solved by technology
Method used
Image
Examples
Embodiment Construction
[0030] In order to make the technical solution of the present invention clearer, the present invention will be described in detail below through specific embodiments in conjunction with the accompanying drawings.
[0031] see Figure 1 ~ Figure 4 The lignite upgrading treatment device of this embodiment includes two hot air passages 1 facing each other, five first heat transfer units 2 arranged between the two hot air passages, each first heat transfer unit includes two rows of heat conduction groups 21, Two rows of heat conduction groups are arranged separately to form a retort gas exhaust channel 22, and two adjacent first heat conduction units are arranged at intervals to form a material channel 3 for the passage of lignite materials;
[0032] Each row of heat conduction groups 21 includes a plurality of first heat conduction pipes 21a arranged substantially along the horizontal direction and first fins 21b connected between two adjacent first heat conduction pipes 21a, and...
PUM
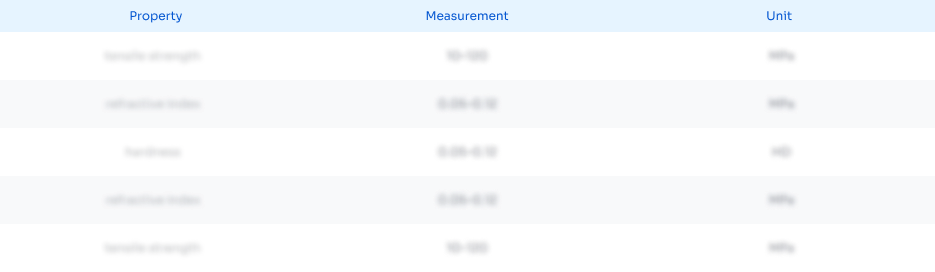
Abstract
Description
Claims
Application Information

- R&D
- Intellectual Property
- Life Sciences
- Materials
- Tech Scout
- Unparalleled Data Quality
- Higher Quality Content
- 60% Fewer Hallucinations
Browse by: Latest US Patents, China's latest patents, Technical Efficacy Thesaurus, Application Domain, Technology Topic, Popular Technical Reports.
© 2025 PatSnap. All rights reserved.Legal|Privacy policy|Modern Slavery Act Transparency Statement|Sitemap|About US| Contact US: help@patsnap.com