Technological process of water droplet pattern layer
A process flow and water drop technology, applied in metal material coating process, coating, ion implantation plating, etc., can solve the problems of different sizes, inability to make a perfect water drop effect layer, uneven water drop effect, etc. clear-cut effect
- Summary
- Abstract
- Description
- Claims
- Application Information
AI Technical Summary
Problems solved by technology
Method used
Examples
Embodiment Construction
[0020] A kind of water droplet layer technological process, it is characterized in that: comprise the following steps:
[0021] 1) Electrostatically dedust the workpiece;
[0022] 2) Pre-treat the workpiece after electrostatic dust removal: when the material of the workpiece is polypropylene, use blue flame for hair removal treatment, and when the material of the workpiece is ABS or AS, perform spraying and degreasing treatment;
[0023] 3) Spray UV vacuum coating primer on the pre-treated workpiece;
[0024] 4) Place the workpiece after spraying the UV vacuum coating primer in a far-infrared drying tunnel with a temperature of 55±5 degrees for leveling;
[0025] 5) Place the leveled workpiece under an ultraviolet lamp with an output power of 900-1000 mJ for 5-10 seconds to cure the vacuum coating primer;
[0026] 6) Place the workpiece after curing of the vacuum coating primer in a vacuum environment with a vacuum degree of 0.072Mpa for coating;
[0027] 7) Take out the co...
PUM
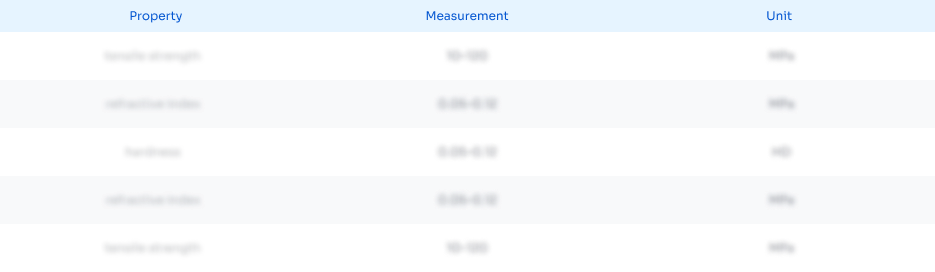
Abstract
Description
Claims
Application Information

- R&D
- Intellectual Property
- Life Sciences
- Materials
- Tech Scout
- Unparalleled Data Quality
- Higher Quality Content
- 60% Fewer Hallucinations
Browse by: Latest US Patents, China's latest patents, Technical Efficacy Thesaurus, Application Domain, Technology Topic, Popular Technical Reports.
© 2025 PatSnap. All rights reserved.Legal|Privacy policy|Modern Slavery Act Transparency Statement|Sitemap|About US| Contact US: help@patsnap.com