Organic electroluminescent display (OLED), manufacturing method thereof and display device
An electroluminescence display and display panel technology, applied in circuits, electrical components, electrical solid devices, etc., can solve the problems affecting the uniformity of the film layer, uneven spreading, disconnection of the cathode 70, etc., to ensure the uniformity of the film layer. , Improve the luminous performance and avoid the effect of color mixing
- Summary
- Abstract
- Description
- Claims
- Application Information
AI Technical Summary
Problems solved by technology
Method used
Image
Examples
example 1
[0059] Example 1: If Figure 4 As shown, the specific steps for making an organic electroluminescent display panel are as follows:
[0060] S201. Coating a layer of lyophobic material with a negative photoresist property on the base substrate 100, such as Figure 6a shown;
[0061] S202. Use the first mask to pattern the lyophobic material with negative photoresist properties by exposure, development and etching to form the pattern of the first pixel defining layer structure 210. At this time, because of the negative photoresist The lyophobic material of the glue nature is formed into a material insoluble in the developer after exposure, while the unexposed material dissolves in the developer, thereby forming the pattern of the first pixel defining layer structure, and because the negative photoresist As the thickness increases, the photoresist material closer to the base substrate receives less light intensity, so the pattern of the formed first pixel defining layer structu...
example 2
[0065] Example 2: If Figure 5 As shown, the specific steps for making the pixel defining layer of the organic electroluminescence display panel are as follows:
[0066] Steps S301 and S302 are completely the same as steps S201 and S202 in Example 1, and will not be repeated here.
[0067] S303, coating a layer of lyophilic material with positive photoresist properties on the base substrate 100 formed with the first pixel defining layer structure 210, at this time the lyophilic material completely covers the first pixel defining layer structure 210 , that is, the upper surface of the first pixel defining layer structure 210 is also covered with a lyophilic material, such as Figure 7a shown;
[0068] S304. Pattern the lyophilic material with positive photoresist properties, and form the pattern of the second pixel defining layer structure 220 by means of exposure, development and etching, wherein the first pixel defining layer structure 210 is covered during etching The lyo...
PUM
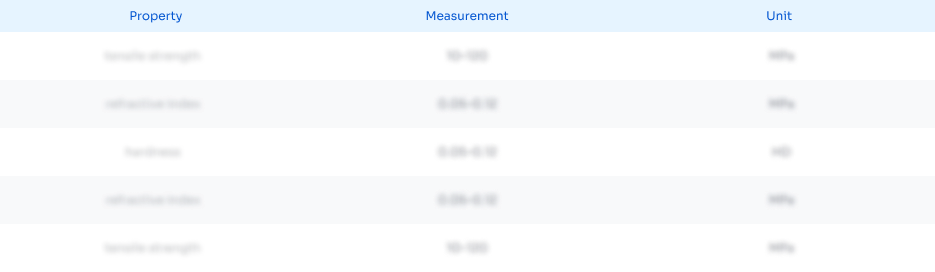
Abstract
Description
Claims
Application Information

- R&D Engineer
- R&D Manager
- IP Professional
- Industry Leading Data Capabilities
- Powerful AI technology
- Patent DNA Extraction
Browse by: Latest US Patents, China's latest patents, Technical Efficacy Thesaurus, Application Domain, Technology Topic, Popular Technical Reports.
© 2024 PatSnap. All rights reserved.Legal|Privacy policy|Modern Slavery Act Transparency Statement|Sitemap|About US| Contact US: help@patsnap.com