Non-contact high-precision calibration method of tool coordinate system of single robot
A technology of tool coordinate system and calibration method, which is applied in the calibration field of industrial robots, and can solve problems such as inability to complete calibration of the robot tool body, affecting accurate control of robot pose, robot parametric programming, and uncontrollability
- Summary
- Abstract
- Description
- Claims
- Application Information
AI Technical Summary
Problems solved by technology
Method used
Image
Examples
Embodiment Construction
[0148] The present invention adopts the calibration finger tooling installed with the measuring ball, and installs the calibration finger tooling on the robot flange or the tool body; uses the laser measuring instrument to measure the center of the measuring ball (that is, the center point of the measuring ball as the calibration point); The laser measuring instrument has a coordinate system of the laser measuring instrument. The data measured by the laser measuring instrument are processed through the algorithm of coordinate transformation, and the relationship between the coordinate system of the laser measuring instrument and the base coordinate system of the robot and the workpiece coordinate system are respectively established to construct The relationship between the robot's base coordinate system and the workpiece coordinate system and the relationship between the tool coordinate system and the robot end coordinate system, so as to perform non-contact high-precision calib...
PUM
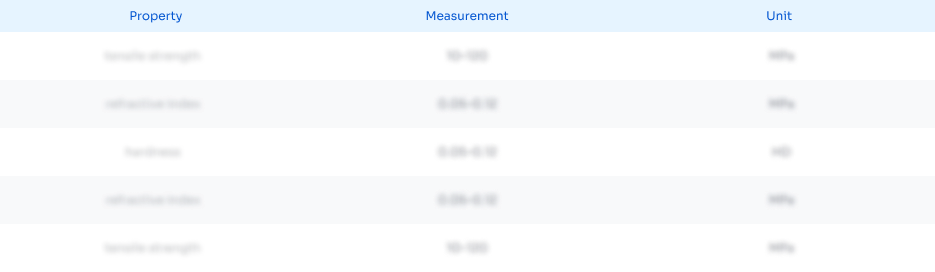
Abstract
Description
Claims
Application Information

- R&D
- Intellectual Property
- Life Sciences
- Materials
- Tech Scout
- Unparalleled Data Quality
- Higher Quality Content
- 60% Fewer Hallucinations
Browse by: Latest US Patents, China's latest patents, Technical Efficacy Thesaurus, Application Domain, Technology Topic, Popular Technical Reports.
© 2025 PatSnap. All rights reserved.Legal|Privacy policy|Modern Slavery Act Transparency Statement|Sitemap|About US| Contact US: help@patsnap.com