Non-damping winding permanent-magnet synchronous motor grid connection method
A permanent magnet synchronous, non-damping technology, applied in the field of motor grid connection, can solve the problems of not having the power frequency operation ability of the grid, and achieve the effect of saving the capacity of the inverter, expanding the application field, and high success rate
- Summary
- Abstract
- Description
- Claims
- Application Information
AI Technical Summary
Problems solved by technology
Method used
Image
Examples
specific Embodiment approach 1
[0035] Specific implementation mode one: the following combination Figure 1 to Figure 7 Describe this embodiment, the grid connection method of permanent magnet synchronous motor with no damping winding described in this embodiment, the grid connection method is realized based on the frequency converter 1, the voltage acquisition board 2, the first contactor 3 and the second contactor 4,
[0036] The voltage acquisition board 2 is used to collect the frequency, amplitude and phase of the grid voltage, and provide it to the frequency converter 1. The three-phase incoming lines R, S, and T of the grid are connected to the permanent magnet synchronous motor with no damping winding in two ways. The first The first road is connected to the permanent magnet synchronous motor without damping winding through the frequency converter 1 and the first contactor 3 in turn, and the second road is connected to the permanent magnet synchronous motor without damping winding through the second ...
specific Embodiment approach 2
[0042] Specific implementation mode two: the following combination Figure 7 This embodiment will be described. This embodiment will further explain Embodiment 1. The method for switching a permanent magnet synchronous motor with no damping winding from the power grid operation state to the inverter 1 operation state is as follows:
[0043] First, through the control of the frequency converter 1, the opening time of the second contactor 4 is earlier than the closing time of the first contactor 3, and then the rotor position of the permanent magnet synchronous motor with no damping winding is tracked online, and the rotor position information is provided to the frequency converter 1, The frequency converter 1 is started to run, thereby realizing the switching of the non-damping winding permanent magnet synchronous motor from the power grid operation state to the operation state of the frequency converter 1 .
[0044] In the operation process of this embodiment, the contactor is...
specific Embodiment approach 3
[0047] Specific implementation mode three: the following combination Figure 1 to Figure 7 Describe this embodiment, the grid connection method of permanent magnet synchronous motor with no damping winding in this embodiment, the grid connection method is based on frequency converter 1, voltage acquisition board 2, first contactor 3, second contactor 4 and reactor 5 achieved,
[0048] The voltage acquisition board 2 is used to collect the frequency, amplitude and phase of the grid voltage, and provide it to the frequency converter 1. The three-phase incoming lines R, S, and T of the grid are connected to the permanent magnet synchronous motor with no damping winding in two ways. The first The first road is connected to the permanent magnet synchronous motor without damping winding through the frequency converter 1, the reactor 5 and the first contactor 3 in turn, and the second road is connected to the permanent magnet synchronous motor without damping winding through the seco...
PUM
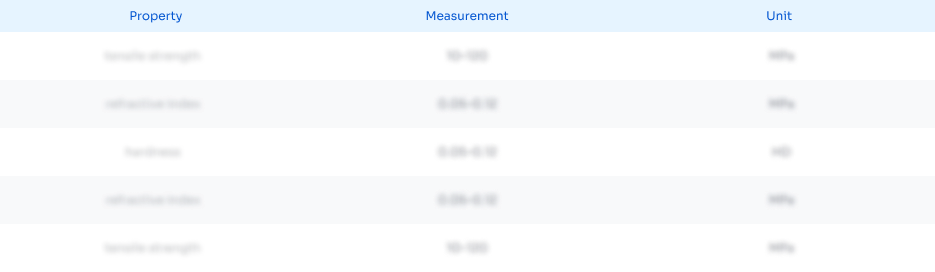
Abstract
Description
Claims
Application Information

- R&D Engineer
- R&D Manager
- IP Professional
- Industry Leading Data Capabilities
- Powerful AI technology
- Patent DNA Extraction
Browse by: Latest US Patents, China's latest patents, Technical Efficacy Thesaurus, Application Domain, Technology Topic, Popular Technical Reports.
© 2024 PatSnap. All rights reserved.Legal|Privacy policy|Modern Slavery Act Transparency Statement|Sitemap|About US| Contact US: help@patsnap.com