Preparation method of enzymolysis lignin-based phenolic resin
A technology for enzymatically decomposing lignin and phenolic resin, applied in the field of phenolic resin preparation, can solve the problems of low lignin reactivity and low substitution rate, achieve environmental safety and pollution-free, increase reactivity, and simple activation modification process Effect
- Summary
- Abstract
- Description
- Claims
- Application Information
AI Technical Summary
Problems solved by technology
Method used
Examples
Embodiment 1
[0011] 20.85g phenol, 22.66g activated modified enzymatic lignin, 16.65mL formaldehyde solution, 2.78g sodium hydroxide and 30mL distilled water were reacted at 80°C for 1h; then 16.65mL formaldehyde solution and 2.78g sodium hydroxide were added, and continued to React at 80°C for 1 hour; add 16.65mL of formaldehyde solution, 2.78g of sodium hydroxide and react at 80°C for 1 hour, quickly cool the reaction system to 40°C, add 4mL of 5% sodium bisulfite solution, and stir to get the enzymatic lignin base Phenolic Resin. The substitution rate of enzymatic lignin to phenol in this product is 52%, the solid content of the adhesive is 47%, the free aldehyde content is 0.25%, and the bonding strength is 1.49MPa.
Embodiment 2
[0013] Put 20.22g of phenol, 38.89g of activated modified enzymatic lignin, 19.05mL of formaldehyde solution, 3.98g of sodium hydroxide and 45mL of distilled water at 80°C for 1 hour; then add 19.05mL of formaldehyde solution, 3.98g of sodium hydroxide, continue to React at 80°C for 1 hour; add 19.05mL of formaldehyde solution, 3.98g of sodium hydroxide and react at 80°C for 1 hour, quickly cool the reaction system to 40°C, add 7mL of 10% calcium bisulfite solution to get the enzymatically hydrolyzed lignin-based phenolic resin . The substitution rate of phenol by enzymatic lignin in this product is 66%, the solid content of the adhesive is 45%, the free aldehyde content is 0.26%, and the bonding strength is 1.38MPa.
PUM
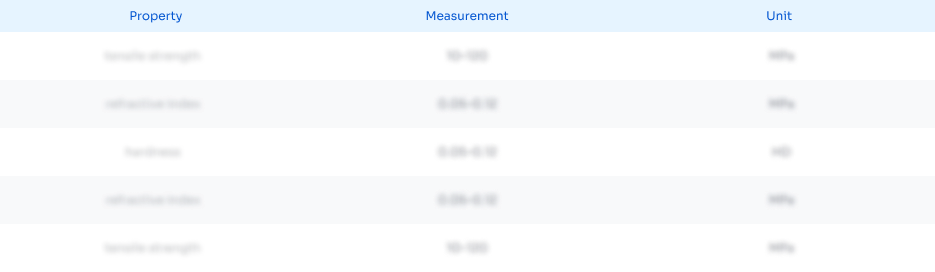
Abstract
Description
Claims
Application Information

- R&D Engineer
- R&D Manager
- IP Professional
- Industry Leading Data Capabilities
- Powerful AI technology
- Patent DNA Extraction
Browse by: Latest US Patents, China's latest patents, Technical Efficacy Thesaurus, Application Domain, Technology Topic, Popular Technical Reports.
© 2024 PatSnap. All rights reserved.Legal|Privacy policy|Modern Slavery Act Transparency Statement|Sitemap|About US| Contact US: help@patsnap.com