Temperature control device for refining metal solidification structure by use of pulse current
A temperature control device, metal solidification technology, applied in the direction of temperature control, non-electric variable control, control/regulation system, etc., can solve the problem of lack of precise control and measurement records of molten metal temperature, and achieve controllability and controllability Repeatability, simple operation, automatic collection and storage
- Summary
- Abstract
- Description
- Claims
- Application Information
AI Technical Summary
Problems solved by technology
Method used
Image
Examples
Embodiment 1
[0022]The temperature control device used for pulse current refinement of metal solidification structure described in this embodiment, the device includes temperature measuring thermocouple I1, temperature measuring thermocouple II2, temperature measuring thermocouple III3, heat insulating asbestos 4, tubular resistance furnace Body Ⅰ5, ceramic support tube 6, heat-resistant ceramic tube Ⅰ7, air outlet 8, water glass sand Ⅰ9, electrode 10, compensation wire Ⅰ11, water glass sand Ⅱ12, heat-resistant ceramic tube Ⅱ13, tubular resistance furnace body Ⅱ14, high pressure Pulse power supply 15, air intake hole 17, temperature control and data acquisition device 18, compensation wire II19, compensation wire III20, compensation wire IV21, displacement and guiding device I22, displacement and guiding device II23, displacement and guiding device III24, thermoelectricity measurement Couple I1, temperature measuring thermocouple II2, and temperature measuring thermocouple III3 are installe...
Embodiment 2
[0027] The device includes temperature measuring thermocouple Ⅰ1, temperature measuring thermocouple Ⅱ2, temperature measuring thermocouple Ⅲ3, heat insulation asbestos 4, tubular resistance furnace body Ⅰ5, ceramic support tube 6, heat-resistant ceramic tube Ⅰ7, air outlet 8, water Glass sand I9, electrode 10, compensation wire I11, water glass sand II12, heat-resistant ceramic tube II13, tubular resistance furnace body II14, high-voltage pulse power supply 15, air inlet 17, temperature control and data acquisition device 18, compensation wire Ⅱ19, compensation wire Ⅲ20, compensation wire Ⅳ21, displacement and guiding device Ⅰ22, displacement and guiding device Ⅱ23, displacement and guiding device Ⅲ24, temperature measuring thermocouple Ⅰ1, temperature measuring thermocouple Ⅱ2, and temperature measuring thermocouple Ⅲ3 are respectively installed in the displacement and guiding device On the guide device I22, the displacement and guide device II23, and the displacement and gui...
Embodiment 3
[0033] The temperature control device used for pulse current refinement of metal solidification structure described in this embodiment, the device includes temperature measuring thermocouple I1, temperature measuring thermocouple II2, temperature measuring thermocouple III3, heat insulating asbestos 4, tubular resistance furnace Body Ⅰ5, ceramic support tube 6, heat-resistant ceramic tube Ⅰ7, air outlet 8, water glass sand Ⅰ9, electrode 10, compensation wire Ⅰ11, water glass sand Ⅱ12, heat-resistant ceramic tube Ⅱ13, tubular resistance furnace body Ⅱ14, high pressure Pulse power supply 15, air intake hole 17, temperature control and data acquisition device 18, compensation wire II19, compensation wire III20, compensation wire IV21, displacement and guiding device I22, displacement and guiding device II23, displacement and guiding device III24, thermoelectricity measurement Couple I1, temperature measuring thermocouple II2, and temperature measuring thermocouple III3 are install...
PUM
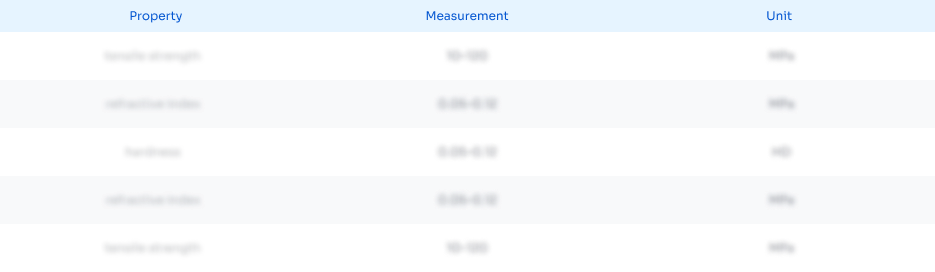
Abstract
Description
Claims
Application Information

- Generate Ideas
- Intellectual Property
- Life Sciences
- Materials
- Tech Scout
- Unparalleled Data Quality
- Higher Quality Content
- 60% Fewer Hallucinations
Browse by: Latest US Patents, China's latest patents, Technical Efficacy Thesaurus, Application Domain, Technology Topic, Popular Technical Reports.
© 2025 PatSnap. All rights reserved.Legal|Privacy policy|Modern Slavery Act Transparency Statement|Sitemap|About US| Contact US: help@patsnap.com