Method for pyrolysis of organosilicone high-boiling substance under catalysis of solid alkali
A catalytic cracking, high boiler technology, applied in chemical instruments and methods, organic chemistry, chemical/physical processes, etc., can solve the problems of non-reusability, increase production costs, etc., achieve less by-products, improve conversion rate, catalyst active effect
- Summary
- Abstract
- Description
- Claims
- Application Information
AI Technical Summary
Problems solved by technology
Method used
Examples
Embodiment 1
[0020] Step (1) in 500L reactor, add tri-n-butylamine 100Kg, dioctadecyl secondary amine 0.1Kg, perfluorotriethylamine 0.1Kg and macroporous cross-linked polyhydroxyethyl methacrylate resin 80Kg respectively, in React at 70°C for 10 h to obtain a composite catalyst, which is ready for use.
[0021] Step (2) Add 100Kg of organosilicon high boilers after impurity removal and 8Kg of high boiler composite catalysts in a 500L cracking kettle with a fractionation tower, then feed hydrogen chloride gas to control the molar ratio of high boilers and hydrogen chloride feed The ratio is 1:1.25, the temperature is raised to 110°C, and after 40 hours of constant temperature under normal pressure, the reaction produces four monochlorosilanes: dimethyldichlorosilane, trimethylchlorosilane, monomethyldichlorosilane, and monomethyltrichlorosilane. The solid-based mixed product is condensed and collected by the overhead condenser of the fractionation column. The conversion rate and the conten...
Embodiment 2
[0023] (1) Add tri-n-butylamine 100Kg, dioctadecyl secondary amine 0.05Kg, perfluorotriethylamine 0.05Kg and macroporous cross-linked polyhydroxyethyl methacrylate resin 50Kg respectively in 500L reactor. React at 30°C for 20 hours to obtain a composite catalyst, which is ready for use.
[0024] (2) Add 100Kg of organosilicon high boilers and 8Kg of composite catalyst after impurity removal in a 500L cracking kettle with a fractionation tower, then feed hydrogen chloride gas, and control the molar ratio of high boilers and hydrogen chloride feed to be 1: 1.05 , heated up to 100°C, and kept at constant temperature for 50 hours under normal pressure, the reaction produced dimethyldichlorosilane, trimethylmonochlorosilane, monomethyldichlorosilane, and monomethyltrichlorosilane. The mixed products are condensed and collected by the overhead condenser of the fractionation column. The conversion rate and the content of dimethyldichlorosilane are shown in Table 1.
Embodiment 3
[0026] 1) In a 500L reactor, add 100Kg of tri-n-butylamine, 0.2Kg of dioctadecyl secondary amine, 0.5Kg of perfluorotriethylamine and macroporous cross-linked polyhydroxyethyl methacrylate resin by mass ratio of 100Kg, React at 100° C. for 5 h to obtain a composite catalyst for future use.
[0027] (2) Add 100Kg of organosilicon high boilers after impurity removal and 8Kg of composite catalyst in a 500L cracking kettle with a fractionation tower, then feed hydrogen chloride gas, and control the molar ratio of high boilers and hydrogen chloride feed to be 1: 1.4 , heated up to 120°C, and kept at constant temperature for 30 hours under normal pressure, the reaction produced dimethyldichlorosilane, trimethylmonochlorosilane, monomethyldichlorosilane, and monomethyltrichlorosilane. The mixed products are condensed and collected by the overhead condenser of the fractionation column. The conversion rate and the content of dimethyldichlorosilane are shown in Table 1.
PUM
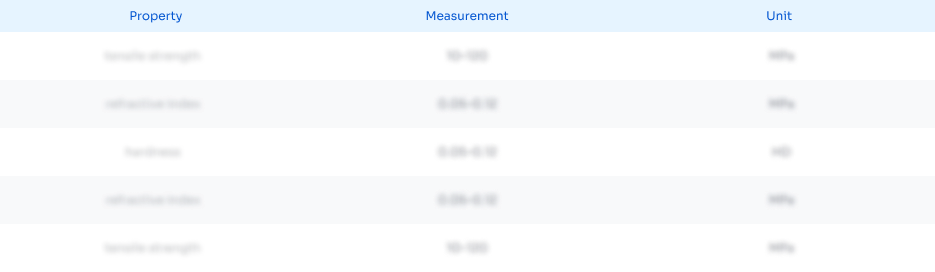
Abstract
Description
Claims
Application Information

- R&D
- Intellectual Property
- Life Sciences
- Materials
- Tech Scout
- Unparalleled Data Quality
- Higher Quality Content
- 60% Fewer Hallucinations
Browse by: Latest US Patents, China's latest patents, Technical Efficacy Thesaurus, Application Domain, Technology Topic, Popular Technical Reports.
© 2025 PatSnap. All rights reserved.Legal|Privacy policy|Modern Slavery Act Transparency Statement|Sitemap|About US| Contact US: help@patsnap.com