Relay capable of adjusting mechanical parameters and device and method for measuring fusion welding force of relay
A technology of mechanical parameters and relays, applied in the field of electrical contact, can solve the problems that the breaking speed cannot reach the relays, the relays cannot be directly measured, and the structural parameters of the relays cannot be applied.
- Summary
- Abstract
- Description
- Claims
- Application Information
AI Technical Summary
Problems solved by technology
Method used
Image
Examples
specific Embodiment approach 1
[0026] Specific implementation mode 1, refer to Figure 1 to Figure 8 Describe this embodiment in detail, the relay with adjustable mechanical parameters described in this embodiment includes a test relay and its fixing device 1, a contact opening distance adjustment device 2, a magnetic gap adjustment device 3, a mechanical reaction force adjustment mechanism 4, Contact speed measuring device 5 and vibration isolation base 6;
[0027] The center position of the vibration isolation base 6 is fixed with a two-dimensional plane slide 11, the test relay and its fixing device 1 are fixed on the two-dimensional plane slide 11, and the two-dimensional plane slide 11 is used to adjust the plane position of the test relay; The opening distance adjustment device 2, the magnetic gap adjustment device 3, the mechanical reaction force adjustment device 4 and the contact speed measurement device 5 are located on the four outer surfaces of the two-dimensional plane sliding table 11 in the c...
specific Embodiment approach 2
[0055] Specific implementation mode two, refer to Figure 9 Describe this embodiment in detail, the measuring device for the welding force of the relay with adjustable mechanical parameters described in Embodiment 1, which includes a resistance voltage divider circuit 37, a signal conditioning circuit 38, a data acquisition and processing circuit 39 and a host computer 40;
[0056] The two ends of the resistance voltage divider circuit 37 are connected in parallel to both sides of the movable contact and the static contact for obtaining the contact voltage; the output end of the resistance voltage divider circuit 37 is connected to the contact voltage signal input end of the signal conditioning circuit 38 ;
[0057] The output end of the piezoelectric quartz force sensor 15 is connected to the force signal input end of the signal conditioning circuit 38; the signal output end of the signal conditioning circuit 38 is connected to the signal input end of the data acquisition pro...
specific Embodiment approach 3
[0059] Specific embodiment three, using the measuring device for the welding force of the relay with adjustable mechanical parameters described in the second specific embodiment to realize the method for measuring the welding force, the method for measuring the welding force includes the following steps:
[0060] Step 1. Adjust the vertical slide of the No. 1 vertical slide 12 to adjust the position of the static contact 21, and adjust the vertical slide of the second vertical slide 25 to adjust the position of the movable contact 20, so that the movable contact 20 and the static contact The size of the contact opening distance between the contacts 21 reaches the setting value of the contact opening distance, adjust the vertical slide of No. 3 vertical slide 30 to adjust the stretching length of the reaction force spring 27;
[0061] Step 2: Start the relay 8 under test, the movable contact 20 and the static contact 21 are energized and closed, and the resistance voltage divide...
PUM
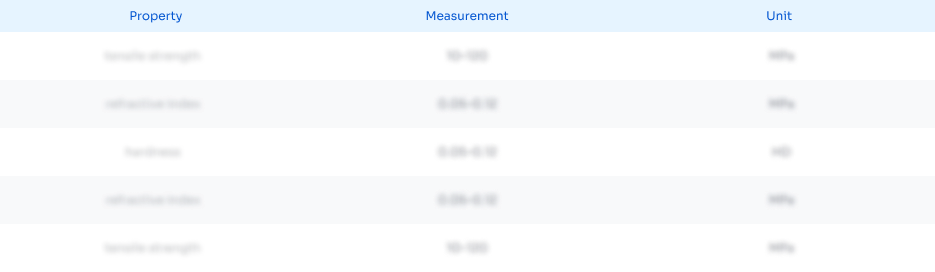
Abstract
Description
Claims
Application Information

- R&D
- Intellectual Property
- Life Sciences
- Materials
- Tech Scout
- Unparalleled Data Quality
- Higher Quality Content
- 60% Fewer Hallucinations
Browse by: Latest US Patents, China's latest patents, Technical Efficacy Thesaurus, Application Domain, Technology Topic, Popular Technical Reports.
© 2025 PatSnap. All rights reserved.Legal|Privacy policy|Modern Slavery Act Transparency Statement|Sitemap|About US| Contact US: help@patsnap.com