Conflict Resolution Method and Optimal Scheduling Method Based on Waiting Time Relaxation
A technology of waiting time and conflict resolution, applied in the direction of total factory control, total factory control, electrical program control, etc., can solve the problems of reducing the effective working time of the converter, lack of goals, and affecting the production efficiency of the converter
- Summary
- Abstract
- Description
- Claims
- Application Information
AI Technical Summary
Problems solved by technology
Method used
Image
Examples
Embodiment Construction
[0074] The present invention will be further described below in conjunction with specific examples and accompanying drawings.
[0075] The conventional converter steelmaking process includes: desulfurization (KR), converter smelting (LD), argon blowing (Ar), ladle furnace (LF), vacuum refining (RH) and continuous casting (CC). The following process prerequisites are met:
[0076] 1) Different steel grades correspond to different process paths, and will go through all or part of the above-mentioned process links in sequence, such as KR→LD→Ar→CC, KR→LD→LF→RH→CC, etc., but there is no loopback on the process path , that is, it will not go through the same process twice, and the situation of returning to furnace and changing steel is not considered here.
[0077] 2) The time of molten steel in the converter steelmaking plant is divided into the following categories: the processing time of the process (including auxiliary time), the transportation time between adjacent processes, ...
PUM
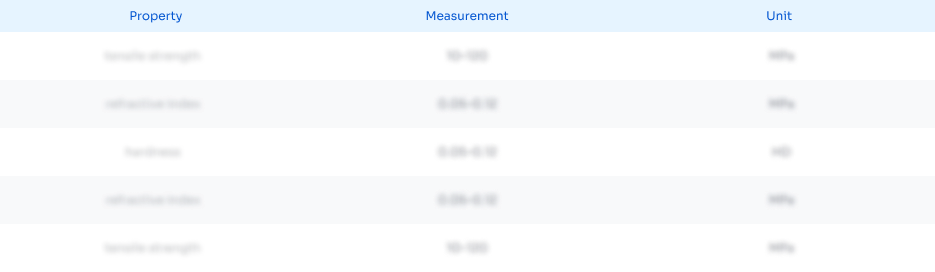
Abstract
Description
Claims
Application Information

- Generate Ideas
- Intellectual Property
- Life Sciences
- Materials
- Tech Scout
- Unparalleled Data Quality
- Higher Quality Content
- 60% Fewer Hallucinations
Browse by: Latest US Patents, China's latest patents, Technical Efficacy Thesaurus, Application Domain, Technology Topic, Popular Technical Reports.
© 2025 PatSnap. All rights reserved.Legal|Privacy policy|Modern Slavery Act Transparency Statement|Sitemap|About US| Contact US: help@patsnap.com