Calibration method of installation error angle between rotating shaft and sensitive shaft of dual-axis rotary inertial navigation system
A technology of installation error angle and dual-axis rotation, which is applied in the field of inertial navigation calibration, can solve the problems of demodulation error, affecting the system attitude accuracy, and the non-coincidence of the gyro sensitive axis and the outer ring rotation axis, so as to eliminate the attitude demodulation Error, the effect of improving the attitude accuracy
- Summary
- Abstract
- Description
- Claims
- Application Information
AI Technical Summary
Problems solved by technology
Method used
Image
Examples
Embodiment Construction
[0030] The present invention is described in detail below in conjunction with specific embodiment:
[0031] The invention proposes a method for calibrating the installation error angle between the rotating shaft and the sensitive shaft of the dual-axis rotary inertial navigation system. Through the calibrating method, it is possible to calibrate the inside and outside of the two rotating shafts inside and outside the dual-axis rotary inertial navigation system and the sensitive shaft. Two installation error angles, after the calibration is completed, the attitude demodulation error caused by the installation error angle is eliminated, and the attitude accuracy of the system is improved.
[0032] There are two types of inner and outer rings in the dual-axis rotary inertial navigation system. One is that the inner ring axis is the yaw axis, and the other is that the outer ring axis is the yaw axis. To facilitate the description of the method, one is assumed here: assuming that t...
PUM
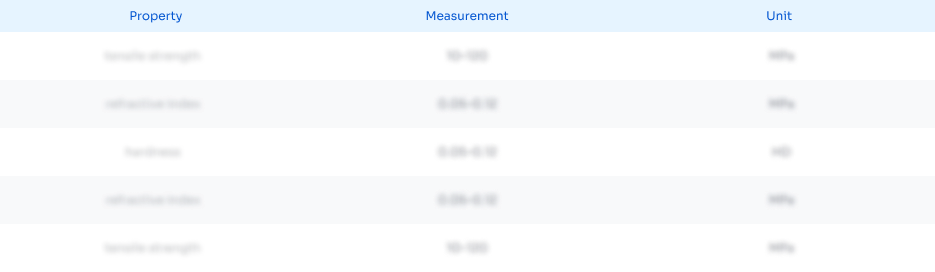
Abstract
Description
Claims
Application Information

- R&D
- Intellectual Property
- Life Sciences
- Materials
- Tech Scout
- Unparalleled Data Quality
- Higher Quality Content
- 60% Fewer Hallucinations
Browse by: Latest US Patents, China's latest patents, Technical Efficacy Thesaurus, Application Domain, Technology Topic, Popular Technical Reports.
© 2025 PatSnap. All rights reserved.Legal|Privacy policy|Modern Slavery Act Transparency Statement|Sitemap|About US| Contact US: help@patsnap.com