Device and method for detecting defects on surface of conical bearing roller
A tapered bearing and detection device technology, which is applied to measurement devices, material analysis by optical means, instruments, etc., can solve the problems of inaccurate manual detection, low detection efficiency, and high detection cost, so as to improve detection efficiency and reduce detection costs. , Overcome the effect of low efficiency
- Summary
- Abstract
- Description
- Claims
- Application Information
AI Technical Summary
Problems solved by technology
Method used
Image
Examples
Embodiment 1
[0034] See attached figure 1 , attached figure 2 , attached image 3 , attached Figure 4 And attached Figure 5 , the tapered bearing roller surface defect detection device of the present invention includes a feed hopper 1, a material channel, a dial 3, a CCD camera 4, an industrial computer 6, a light source 5, a friction wheel 9, a detection table 14, a baffle plate 10, an ejector device 11 and conveyor belt 13;
[0035] The feed hopper 1 is arranged at the inlet end of the feed channel, the inlet end of the feed channel is placed obliquely higher than the outlet end, the dial 3 is arranged above the outlet end of the feed channel, and the dial 3 Intermittently move the tapered bearing rollers;
[0036] The inlet end of the detection platform 14 is connected with the outlet end of the material channel, and the outlet end of the detection platform 14 is provided with a friction wheel 9, and the friction wheel 9 cooperates with the tapered bearing roller at the outlet e...
Embodiment 2
[0050] The difference between this embodiment and the first embodiment is that: the material channel is a trapezoidal material channel, and the inclination angle of the upper surface of the trapezoidal material channel is the same as the cone angle of one-half of the tapered bearing rollers.
PUM
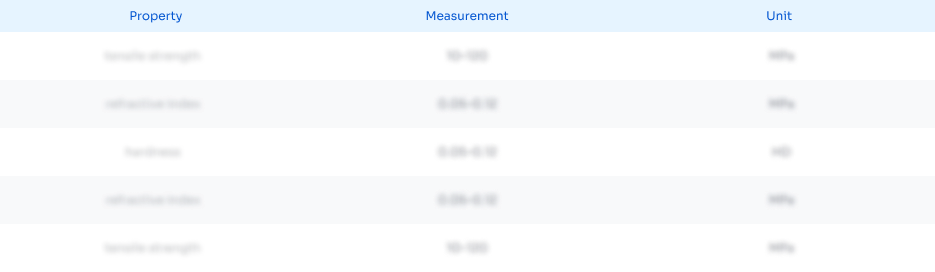
Abstract
Description
Claims
Application Information

- R&D
- Intellectual Property
- Life Sciences
- Materials
- Tech Scout
- Unparalleled Data Quality
- Higher Quality Content
- 60% Fewer Hallucinations
Browse by: Latest US Patents, China's latest patents, Technical Efficacy Thesaurus, Application Domain, Technology Topic, Popular Technical Reports.
© 2025 PatSnap. All rights reserved.Legal|Privacy policy|Modern Slavery Act Transparency Statement|Sitemap|About US| Contact US: help@patsnap.com