Plastic sleeve separation die of reverser
A commutator, plastic sleeve technology, applied in the field of molds, can solve the problems of high labor intensity and low efficiency
- Summary
- Abstract
- Description
- Claims
- Application Information
AI Technical Summary
Problems solved by technology
Method used
Image
Examples
Embodiment Construction
[0013] As shown in the figure, the commutator plastic sleeve separation mold of the present invention includes a movable upper mold 1 and a fixed lower mold, and a thimble 3 is installed on the bottom of the movable upper mold 1, and the diameter of the head of the thimble 3 is smaller than the diameter of the inner hole of the plastic sleeve 5. The head of the thimble 3 has a curved surface matching the shape of the upper end surface of the commutator 6 and is provided with a plunger 4 for positioning the inner hole of the commutator 6. The fixed lower mold includes an upper backing plate 8 and a lower backing plate 9 fixedly connected , the upper backing plate 8 is provided with the upper through hole 11 that allows the commutator 6 and the plastic cover 5 combination to pass through simultaneously, the diameter of the upper through hole 11 is greater than the diameter of the outer circle of the plastic cover 5, and the lower backing plate 9 is provided with the commutator 6 ...
PUM
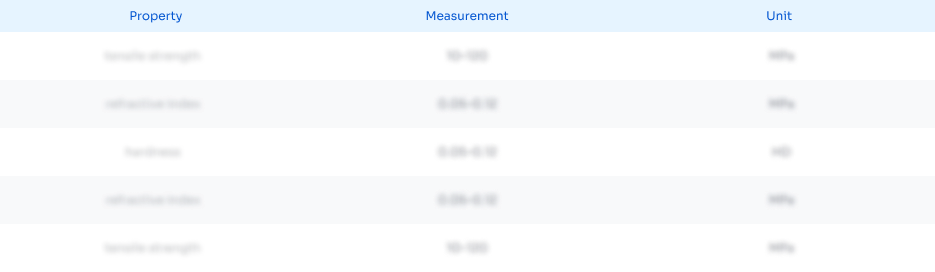
Abstract
Description
Claims
Application Information

- R&D
- Intellectual Property
- Life Sciences
- Materials
- Tech Scout
- Unparalleled Data Quality
- Higher Quality Content
- 60% Fewer Hallucinations
Browse by: Latest US Patents, China's latest patents, Technical Efficacy Thesaurus, Application Domain, Technology Topic, Popular Technical Reports.
© 2025 PatSnap. All rights reserved.Legal|Privacy policy|Modern Slavery Act Transparency Statement|Sitemap|About US| Contact US: help@patsnap.com