Hollow shaft outer circle grinding high-precision spring plug
A high-precision technology for grinding outer circles, applied in grinding machines, grinding workpiece supports, grinding/polishing equipment, etc., can solve problems such as failure to meet design requirements, difficulty in interference fit and disassembly, waste of time and materials, etc. The effect of improving quality and economic benefit, high product quality and simple operation
- Summary
- Abstract
- Description
- Claims
- Application Information
AI Technical Summary
Problems solved by technology
Method used
Image
Examples
Embodiment Construction
[0008] In the figure: 1 plugging core, 2 spring sleeve, 3 rear cover, 4 adjusting bolt, 5 workpiece.
[0009] The present invention is composed of a plugging core 1, a spring sleeve 2, a rear cover 3, and an adjusting bolt 4; the plugging core 1 is a stepped shaft with a shoulder, and the shaft shoulder is provided with a drive bolt threaded hole, and the end surface of the shaft shoulder is provided with a weight-reducing groove. The outer circle of the small end of the plugging core 1 is provided with a tapered surface, and 4 threaded holes are evenly distributed on the end surface, and the center of the two ends of the plugging core 1 is provided with a top hole; the taper of the inner hole of the spring sleeve 2 is consistent with the outer conicity of the plugging core 1, and is processed by matching grinding , the spring sleeve 2 is provided with a workpiece positioning table, the end face A of the positioning table is fitted with the end face of the workpiece 5 holes, an...
PUM
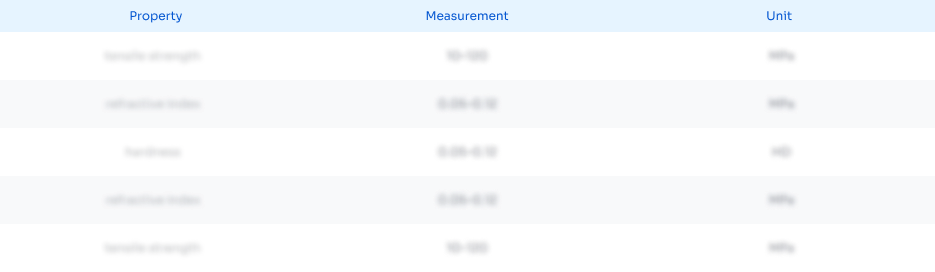
Abstract
Description
Claims
Application Information

- R&D Engineer
- R&D Manager
- IP Professional
- Industry Leading Data Capabilities
- Powerful AI technology
- Patent DNA Extraction
Browse by: Latest US Patents, China's latest patents, Technical Efficacy Thesaurus, Application Domain, Technology Topic, Popular Technical Reports.
© 2024 PatSnap. All rights reserved.Legal|Privacy policy|Modern Slavery Act Transparency Statement|Sitemap|About US| Contact US: help@patsnap.com