A kind of printing burnishing treatment agent for synthetic leather and preparation method thereof
A technology for synthetic leather and treatment agent, which is applied in fiber treatment, textiles and papermaking, etc., can solve the problems of poor comprehensive treatment effect, high manufacturing cost of treatment reagents, and inability to satisfy consumers' perception of synthetic leather, and achieve superior leather texture. , Good oily effect, the effect of increasing production cost
- Summary
- Abstract
- Description
- Claims
- Application Information
AI Technical Summary
Problems solved by technology
Method used
Examples
Embodiment 1
[0022] The printing burnishing treatment agent for synthetic leather consists of the following components: 20 parts by weight of modified polyurethane, 25 parts by weight of dimethylformamide, 29 parts by weight of butyl ester, 7 parts by weight of silica matting powder, and discoloration powder 6 parts by weight, 1 part by weight of epoxy soybean oil, 1 part by weight of water repellant, and 0.2 parts by weight of dispersant.
[0023] The preparation method of the above-mentioned printed burnishing treatment agent for synthetic leather is: under normal temperature and pressure, 10 parts by weight of modified polyurethane, 25 parts by weight of dimethylformamide, 29 parts by weight of butyl ester, 7 parts by weight of Silica matting powder, 6 parts by weight of color changing powder are mixed, stirred for at least 30 minutes until the mixture is evenly mixed; 1 part by weight of epoxy soybean oil, 1 part by weight of water repellent, 0.2 parts by weight of The dispersant is st...
Embodiment 2
[0026] The printing burnishing treatment agent for synthetic leather consists of the following components: 24 parts by weight of modified polyurethane, 28 parts by weight of dimethylformamide, 33 parts by weight of butyl ester, 10 parts by weight of silica matting powder, and discoloration powder 10 parts by weight, 4 parts by weight of epoxy soybean oil, 3 parts by weight of water repellant, and 1 part by weight of dispersant.
[0027] The preparation method of the above-mentioned printed burnishing treatment agent for synthetic leather is: under normal temperature and pressure, 12 parts by weight of modified polyurethane, 28 parts by weight of dimethylformamide, 33 parts by weight of butyl ester, 10 parts by weight of Silica matting powder, 10 parts by weight of color changing powder are mixed, stirred for at least 30 minutes until the mixture is evenly mixed; 4 parts by weight of epoxy soybean oil, 3 parts by weight of water repellent, 1 part by weight of Stir the dispersan...
Embodiment 3
[0030] The printing burnishing treatment agent for synthetic leather consists of the following components: 22 parts by weight of modified polyurethane, 26.5 parts by weight of dimethylformamide, 31 parts by weight of butyl ester, 8.5 parts by weight of silica matting powder, and discoloration powder 8 parts by weight, 2 parts by weight of epoxy soybean oil, 1.5 parts by weight of water repellant, and 0.5 parts by weight of dispersant.
[0031] The preparation method of the above-mentioned printing burnishing treatment agent for synthetic leather is: under normal temperature and pressure, 11 parts by weight of modified polyurethane, 26.5 parts by weight of dimethylformamide, 31 parts by weight of butyl ester, 8.5 parts by weight of Silica matting powder, 8 parts by weight of color changing powder are mixed, stirred for at least 30 minutes until the mixture is evenly mixed; 2 parts by weight of epoxy soybean oil, 1.5 parts by weight of water repellent, 0.5 parts by weight of The...
PUM
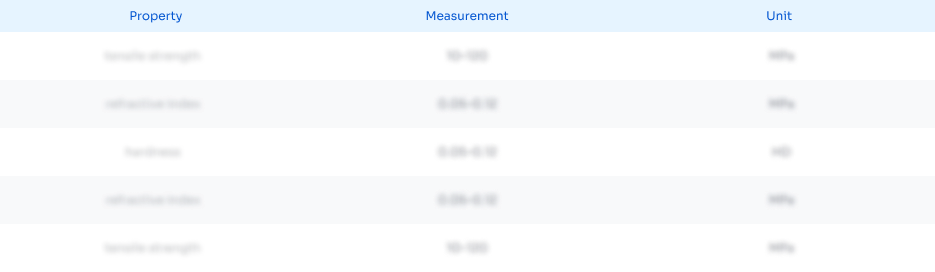
Abstract
Description
Claims
Application Information

- R&D Engineer
- R&D Manager
- IP Professional
- Industry Leading Data Capabilities
- Powerful AI technology
- Patent DNA Extraction
Browse by: Latest US Patents, China's latest patents, Technical Efficacy Thesaurus, Application Domain, Technology Topic, Popular Technical Reports.
© 2024 PatSnap. All rights reserved.Legal|Privacy policy|Modern Slavery Act Transparency Statement|Sitemap|About US| Contact US: help@patsnap.com