A planar two-dimensional time grating displacement sensor
A technology of displacement sensor and plane 2, which is applied in the direction of instruments, measuring devices, and electric devices, etc. It can solve the problems of high cost, Abbe error of the measurement system, occupying a large space, etc., and achieves strong shock and vibration capabilities and resistance to oil and dust Strong, Simple Effects
- Summary
- Abstract
- Description
- Claims
- Application Information
AI Technical Summary
Problems solved by technology
Method used
Image
Examples
Embodiment Construction
[0024] The present invention will be further described below in conjunction with the accompanying drawings.
[0025] Such as figure 1 As shown, the sensor of the present invention includes two parts, the fixed array surface 1 and the dynamic array surface 2, which are placed in parallel with a small gap δ.
[0026] The fixed array surface 1 is composed of the fixed array surface substrate and the excitation coils arranged on the surface of the fixed array surface substrate. The fixed array surface substrate is made of magnetically permeable materials, and there are 4 sets of excitation coils, which are respectively the first group of excitation coils 11 and the second group of excitation coils. The coils 12, the third group of exciting coils 13 and the fourth group of exciting coils 14 are arranged in a four-layer structure, and each group of exciting coils is composed of the same linear array of exciting coils. The fixed array surface adopts semiconductor processing technolo...
PUM
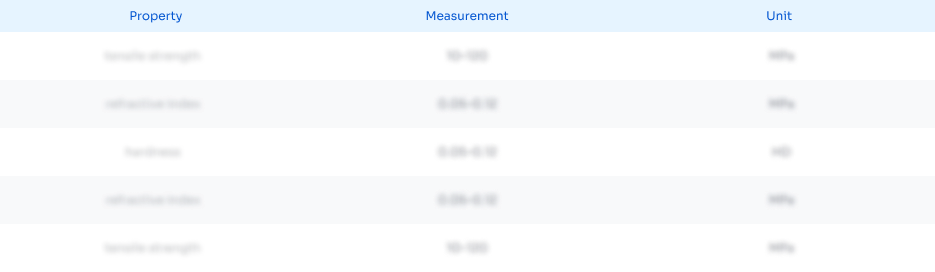
Abstract
Description
Claims
Application Information

- R&D
- Intellectual Property
- Life Sciences
- Materials
- Tech Scout
- Unparalleled Data Quality
- Higher Quality Content
- 60% Fewer Hallucinations
Browse by: Latest US Patents, China's latest patents, Technical Efficacy Thesaurus, Application Domain, Technology Topic, Popular Technical Reports.
© 2025 PatSnap. All rights reserved.Legal|Privacy policy|Modern Slavery Act Transparency Statement|Sitemap|About US| Contact US: help@patsnap.com