Composite early strength agent for foamed cement insulation board and preparation method thereof
A composite early strength agent and foamed cement technology, applied in the field of building materials, can solve the problem of no rapid setting, achieve the effects of rapid strength increase, shorten the initial setting and final setting time, and improve production efficiency
- Summary
- Abstract
- Description
- Claims
- Application Information
AI Technical Summary
Problems solved by technology
Method used
Examples
preparation example Construction
[0018] The preparation method of composite early strength agent for foamed cement insulation board of the present invention comprises the following steps:
[0019] (1) Preparation of component A: by weight percentage, mix 38-45% of quick-setting agent, 1.5-3.0% of metal salt, and 53-60% of water to obtain component A; wherein, the quick-setting The agent can choose one of sodium silicate, aluminum sulfate, aluminum nitrate, and ferric sulfate; the metal salt can choose one or a combination of copper sulfate, potassium dichromate, ferrous sulfate or aluminum potassium sulfate ;
[0020] (2) Preparation of component B: by weight percentage, any one of 60-70% sodium chloride or 60-70% sodium sulfate or 60-70% aluminum chloride, 25-35% Sodium nitrite and 3-7% surfactants are mixed and stirred evenly to obtain component B; wherein, the surfactants are optionally mixed with triethanolamine, calcium formate, acetic acid and acetate, and triisopropanolamine. choose one;
[0021] (3...
Embodiment 1
[0025] Component A of this embodiment consists of the following components: 42g of sodium silicate, 0.6g of copper sulfate, 0.6g of potassium dichromate, 0.6g of aluminum potassium sulfate, and 56.2g of water.
[0026] Component B consists of the following components: 65g sodium chloride, 30g sodium nitrite, 5g triethanolamine.
[0027] The preparation method is as follows:
[0028] (1) Preparation of component A: Mix 42g of sodium silicate, 0.6g of copper sulfate, 0.6g of potassium dichromate, 0.6g of potassium aluminum sulfate, and 56.2g of water to obtain component A;
[0029] (2) Preparation of component B: Mix 65g of sodium chloride, 30g of sodium nitrite, and 5g of triethanolamine and stir evenly to obtain component B;
[0030] (3) Dissolve 1 part of component B in 10 parts (parts by weight) of water, and obtain B solution after fully dissolved;
[0031] (4) Press solution B obtained in step 3 with component A in step 1, solution B: component A = 1:1, and mix evenly to...
Embodiment 2
[0033] Component A of this embodiment consists of the following components: 43g of sodium silicate, 0.7g of copper sulfate, 0.6g of potassium dichromate, 0.7g of aluminum potassium sulfate, and 55g of water.
[0034] Component B consists of the following components: 61g sodium chloride, 32g sodium nitrite, 7g triethanolamine.
[0035] The preparation method is as follows:
[0036] (1) Preparation of component A: Mix 43g of sodium silicate, 0.7g of copper sulfate, 0.6g of potassium dichromate, 0.7g of potassium aluminum sulfate, and 55g of water to obtain component A;
[0037] (2) Preparation of component B: Mix 61g of sodium chloride, 32g of sodium nitrite, and 7g of triethanolamine and stir evenly to obtain component B;
[0038] (3) Dissolve 1 part of component B in 10 parts (parts by weight) of water, and obtain B solution after fully dissolved;
[0039] (4) Press solution B obtained in step 3 with component A in step 1, solution B: component A = 1:1, and mix evenly to obt...
PUM
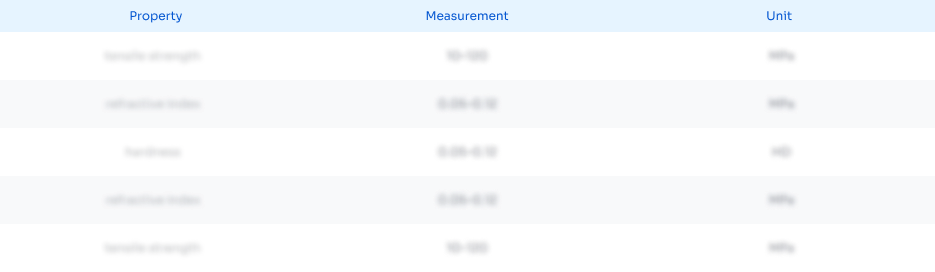
Abstract
Description
Claims
Application Information

- R&D
- Intellectual Property
- Life Sciences
- Materials
- Tech Scout
- Unparalleled Data Quality
- Higher Quality Content
- 60% Fewer Hallucinations
Browse by: Latest US Patents, China's latest patents, Technical Efficacy Thesaurus, Application Domain, Technology Topic, Popular Technical Reports.
© 2025 PatSnap. All rights reserved.Legal|Privacy policy|Modern Slavery Act Transparency Statement|Sitemap|About US| Contact US: help@patsnap.com