Vibration modeling and analyzing method of crack impeller structure of centrifugal compressor
A centrifugal compressor and analysis method technology, applied in special data processing applications, instruments, electrical digital data processing, etc., can solve the problems of high computing hardware level for statistical analysis, unacceptable time required for analysis, etc.
- Summary
- Abstract
- Description
- Claims
- Application Information
AI Technical Summary
Problems solved by technology
Method used
Image
Examples
Embodiment example
[0113] This implementation case combines figure 2 The shown impeller model of a certain centrifugal compressor verifies the effectiveness of the invention, where 1 is the end cover, 2 is the blade, and 3 is the disc.
[0114] A centrifugal impeller structure is welded by end covers, blades and discs. According to engineering experience, fatigue cracks often appear at the welding position between the blades and the end cover on the outer edge of the intake end, and the cracks analyzed in this implementation case are located there. The analysis framework of the cracked impeller structure mainly includes three parts: pre-processing module, analysis module and post-processing module.
[0115] First, the finite element model of the entire impeller structure is obtained by means of rotational transformation, and then the calculation accuracy of the system reduced by the hybrid interface modal synthesis method is verified. When comparing the results, the analyzed object is the impe...
PUM
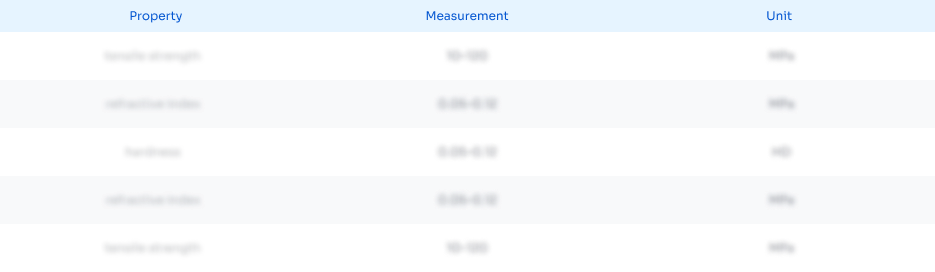
Abstract
Description
Claims
Application Information

- R&D
- Intellectual Property
- Life Sciences
- Materials
- Tech Scout
- Unparalleled Data Quality
- Higher Quality Content
- 60% Fewer Hallucinations
Browse by: Latest US Patents, China's latest patents, Technical Efficacy Thesaurus, Application Domain, Technology Topic, Popular Technical Reports.
© 2025 PatSnap. All rights reserved.Legal|Privacy policy|Modern Slavery Act Transparency Statement|Sitemap|About US| Contact US: help@patsnap.com