Oil tank bracket machining die
A technology for processing molds and brackets, which is used in the field of processing molds for fuel tank brackets, can solve the problems of weakened cross-section and brittle fracture of components, and achieve the effects of reducing workload, improving service life and reducing friction.
- Summary
- Abstract
- Description
- Claims
- Application Information
AI Technical Summary
Problems solved by technology
Method used
Image
Examples
Embodiment 1
[0021] Such as figure 1 and figure 2 As shown, the fuel tank bracket processing mold of the present invention comprises an upper mold base 5 and a lower mold base 7, a punch 4 is installed on the upper mold base 5, a die 1 is installed on the lower die base 7, and the die base 7 is installed on the die base 7. 1 is installed with a forming block 2, the upper surface of the forming block 2 is two interconnected inclined surfaces, the forming block 2 is provided with a forming groove 11, and a discharge cavity 9 is provided in the lower mold base 7. A baffle 10 is installed inside the body 9, and the baffle 10 is connected to the bottom of the discharge cavity 9 through a spring 8, and a discharge rod 3 is installed on the baffle 10, and the discharge rod 3 runs through the lower mold base 7, the die 1 and molding block 2 and are higher than the bottom of molding groove 11. When the present invention is working, the upper die base 5 is separated from the lower die base 7 driv...
Embodiment 2
[0023] Such as figure 1 and figure 2 As shown, this embodiment is based on Embodiment 1, the groove wall of the forming groove 11 is arc-shaped, and the groove width of the forming groove 11 gradually decreases along the vertical direction. The two walls of the forming groove 11 are protruding circular arcs, so that the groove width of the forming groove 11 decreases gradually along the vertical direction, and the smooth circular arc surface can reduce the friction force of the steel plate moving down in the groove and reduce the pressure of the punch 4 times. The resistance to shifting can reduce the workload of the driving equipment during the bending process of the steel plate, and indirectly reduce the production cost.
Embodiment 3
[0025] Such as figure 2 As shown, this embodiment is based on Embodiment 1, the punch 4 is a trapezoidal block matching the forming groove 11, and leveling plates 12 are installed on both sides of the trapezoidal block. The punch 4 matches the profile of the forming groove 11, and the steel plate can be bent into the required shape. The flat plate 12 installed on both sides of the trapezoidal block can make the steel plate form a supporting surface, and the supporting surface increases the bracket and The contact area of the fuel tank ensures the stability of the fuel tank during use.
PUM
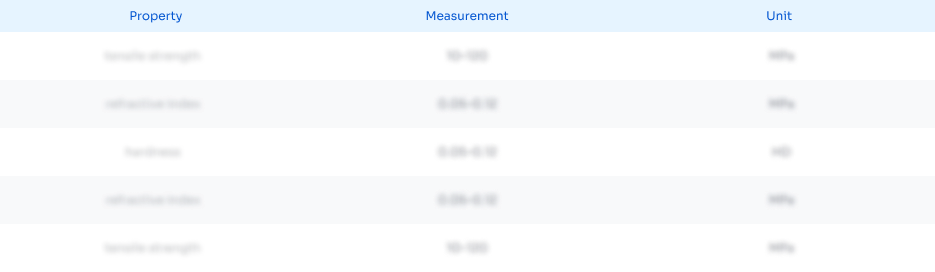
Abstract
Description
Claims
Application Information

- Generate Ideas
- Intellectual Property
- Life Sciences
- Materials
- Tech Scout
- Unparalleled Data Quality
- Higher Quality Content
- 60% Fewer Hallucinations
Browse by: Latest US Patents, China's latest patents, Technical Efficacy Thesaurus, Application Domain, Technology Topic, Popular Technical Reports.
© 2025 PatSnap. All rights reserved.Legal|Privacy policy|Modern Slavery Act Transparency Statement|Sitemap|About US| Contact US: help@patsnap.com