Roller painting reaction and reverse glazing combined process
A light combination and process technology, applied in the printing field, can solve problems such as single process effect and poor hot stamping processability, and achieve the effect of improving packaging grade and processing quality
- Summary
- Abstract
- Description
- Claims
- Application Information
AI Technical Summary
Problems solved by technology
Method used
Image
Examples
Embodiment approach 1
[0029] Embodiment 1: A combined process of roller coating reaction and reverse glazing, which is completed on-line by a printing machine. The printing machine has five printing color groups and two glazing units. Four of the five printing color groups in the printing machine According to the requirements of the printing color sequence, the transfer of yellow, magenta, cyan and black inks is completed, so that the surface of the substrate (such as paper) produces the effect of color printing. The remaining one printing color group is used for the coating of the primer in the graphic area A, the glazing unit I is used for the coating of the primer in the graphic area B, and the glazing unit II is used in the entire graphic area A and the graphic area B is coated with top oil, so that, through the reaction between the primer and the top oil, the wettability of the top oil in the graphic area of the printed primer and the blank area of the unprinted primer is different, and the...
Embodiment approach 2
[0041] Embodiment two: The specific steps of this process are:
[0042] 1) Print four-color inks sequentially on the substrate according to the color sequence, and obtain a printing layer with a color effect on the substrate;
[0043] 2) A printing color group is used to apply the partial primer of the printed matter, and the partial primer application constitutes the graphic area A;
[0044] 3) fully dry or cure;
[0045] 4) The anilox roller of the glazing unit Ⅰ is used to coat the base oil again on the substrate to form a new graphic area B, and the graphic area A and graphic area B do not overlap;
[0046] 5) Fully dry or cure;
[0047] 6) The anilox roller of the glazing unit II coats the surface oil of the printed matter on the substrate to form a graphic area C, and the graphic area A after coating the surface oil forms a reverse glazing area A, and the coated surface The image area B after oiling forms the reverse glazing area B, and the area beyond the image area ...
PUM
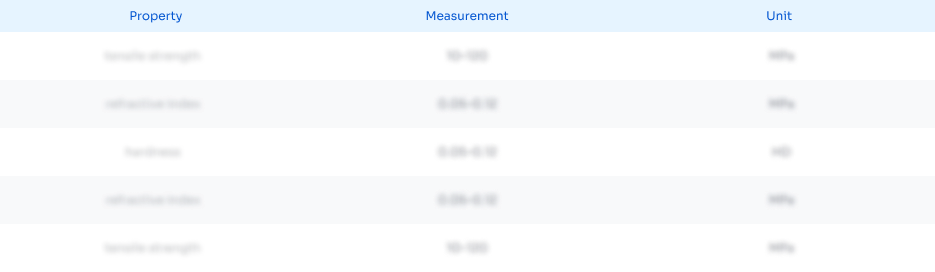
Abstract
Description
Claims
Application Information

- R&D
- Intellectual Property
- Life Sciences
- Materials
- Tech Scout
- Unparalleled Data Quality
- Higher Quality Content
- 60% Fewer Hallucinations
Browse by: Latest US Patents, China's latest patents, Technical Efficacy Thesaurus, Application Domain, Technology Topic, Popular Technical Reports.
© 2025 PatSnap. All rights reserved.Legal|Privacy policy|Modern Slavery Act Transparency Statement|Sitemap|About US| Contact US: help@patsnap.com