Method for measuring optical axis in aspheric surface detection by means of self-aligning plane mirror
A technology for measuring light and plane mirror, applied in the field of optical detection, can solve the problem of low measurement accuracy, and achieve the effect of high accuracy
- Summary
- Abstract
- Description
- Claims
- Application Information
AI Technical Summary
Problems solved by technology
Method used
Image
Examples
Embodiment
[0025] a. Place the plane mirror 2 close to the detected aspheric surface 10 (the farther away from the interferometer 1, the higher the measurement accuracy), and let the parallel light 3 emitted by the interferometer 1 shine on the plane mirror 2 Within the effective aperture; adjust the two angular directions of the yaw and pitch of the plane mirror 2, so that the interference fringes formed in the interferometer 1 are in the state of zero fringes; use the interferometer 1 to measure and analyze, and check the surface shape detection results Tilt amount (tilt item after zernike fitting), and continue to adjust the plane mirror 2 until the tilt is close to 0, and the adjustment is completed to realize the self-alignment of the plane mirror 2 to the interferometer;
[0026] b. Use the target ball of the laser tracker 4 to guide the laser light of the laser tracker 4 to the self-collimating plane mirror 2 and form a reflection, use the target ball to obtain the reflected laser ...
PUM
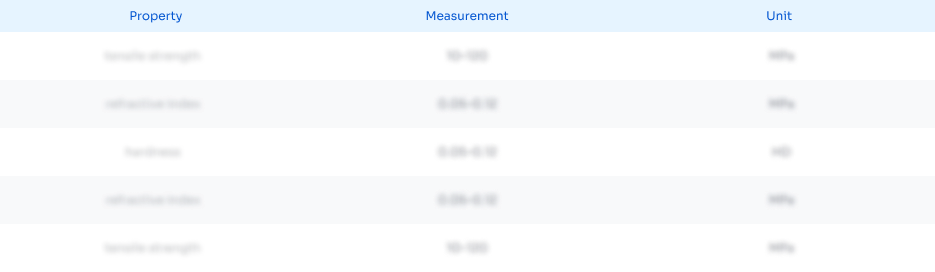
Abstract
Description
Claims
Application Information

- R&D Engineer
- R&D Manager
- IP Professional
- Industry Leading Data Capabilities
- Powerful AI technology
- Patent DNA Extraction
Browse by: Latest US Patents, China's latest patents, Technical Efficacy Thesaurus, Application Domain, Technology Topic, Popular Technical Reports.
© 2024 PatSnap. All rights reserved.Legal|Privacy policy|Modern Slavery Act Transparency Statement|Sitemap|About US| Contact US: help@patsnap.com