Structures for Exhaust Pipe Bending
A technology for exhaust pipes and support frames, which is applied in the field of pipe bending devices, can solve problems such as corrosion, metal fatigue, and environmental pollution, and achieve the effects of ensuring stable movement, ensuring force balance, and prolonging service life
- Summary
- Abstract
- Description
- Claims
- Application Information
AI Technical Summary
Problems solved by technology
Method used
Image
Examples
Embodiment 1
[0024] Such as Figure 1 to Figure 4 As shown, the structure of the present invention for bending exhaust pipes includes a support frame 1, a column 2 is installed on the support frame 1, an annular groove is opened on the column 2, and a hydraulic pressure is installed on the support frame 1. Cylinder 3, the output end of hydraulic cylinder 3 is connected with stopper 5, and described stopper 5 is facing the arc top of annular groove, and semicircle groove 6 is opened on described stopper 5, and the inner wall at both ends of semicircle groove 6 and A roller 10 is installed on the bottom of the groove, and the roller 10 is connected with the semicircular groove 6 through a rotating shaft 16; it also includes a sliding groove 7, which is arranged on the supporting frame 1, and travel switches 8 are installed at both ends of the sliding groove 7 , the travel switch 8 is connected with the control device of the hydraulic cylinder 3 through wires, and a damping structure is also ...
Embodiment 2
[0026] Such as figure 1 and image 3As shown, the present embodiment is based on Embodiment 1, and the damping structure includes a roller 10 support and a support cylinder 11, the support cylinder 11 is fixed in the semicircular groove 6, and the roller 10 is arranged on the roller 10 support through the rotating shaft 16. The bottom of the roller 10 bracket is provided with a support rod 13, the support rod 13 is installed in the support tube 11, the support rod 13 is provided with a limit block 14, and a torsion spring is installed between the limit block 14 and the bottom of the support tube 11 15. When the straight pipe piece 17 of the exhaust pipe is in contact with the two ends of the semicircular groove 6, under the propulsion of the hydraulic cylinder 3, the groove wall of the semicircular groove 6 and the roller 10 on the bottom of the groove begin to apply pressure to the straight pipe piece 17, and at the same time After the deformation of the pipe fitting 17, a ...
Embodiment 3
[0028] Such as image 3 As shown, in this embodiment, on the basis of Embodiment 1, the angle formed by the inner walls of the two ends of the semicircular groove 6 and the axis line of the roller 10 on the bottom of the groove is 60°. The distribution of the three rollers 10 on the semicircular groove 6 directly affects the stress of the straight pipe 17 of the exhaust pipe. The angle formed by the axis lines between the rollers 10 is 60°, so that the straight pipe 17 is placed in the semicircular groove 6. There are three evenly distributed stress points inside, and when the stopper 5 is pushed forward, the force balance of the straight pipe piece 17 is ensured, and indentation on the straight pipe piece 17 is avoided.
PUM
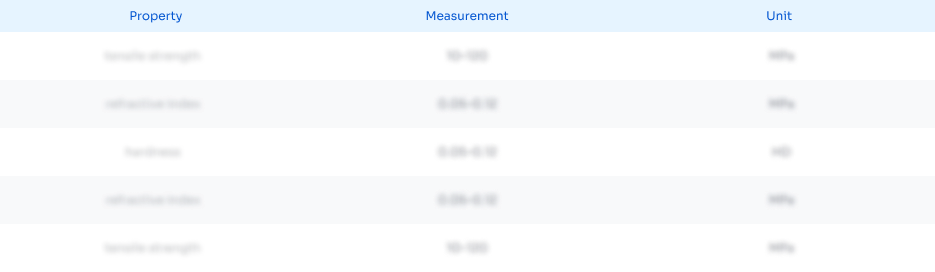
Abstract
Description
Claims
Application Information

- Generate Ideas
- Intellectual Property
- Life Sciences
- Materials
- Tech Scout
- Unparalleled Data Quality
- Higher Quality Content
- 60% Fewer Hallucinations
Browse by: Latest US Patents, China's latest patents, Technical Efficacy Thesaurus, Application Domain, Technology Topic, Popular Technical Reports.
© 2025 PatSnap. All rights reserved.Legal|Privacy policy|Modern Slavery Act Transparency Statement|Sitemap|About US| Contact US: help@patsnap.com